Take a look inside the hub with us in our exclusive Qvist factory tour just outside of Dresden, Germany. A year and a half ago we peeked inside Qvist’s unique all-new double ratchet, high-engagement mountain bike hub concept. Now we peek inside the Qvist CNC machines with idea’s man Roman Elsner – just as they are ramping up – to see how they’re made.
Besides the up close look at high-tech precision German manufacturing. The real added bonus is that the Qvist hubs & complete wheels are now available to pre-order at a 10% off discount. And many more components are on the way, too…
Qvist 3° Double Ratchet 120 POE bike hubs

How hard can it be to make a good bicycle hub, right? Or well, a quick high-engagement, relatively light hub that is also durable. It turns out that it is pretty tough. Qvist had a – now patented – idea for a novel adaptation of the trusted DT-style start ratchet. And they ran with it.
Instead of creating smaller ratchet teeth to add more points of engagement (POEs), they doubled the speed of hub engagement by machining teeth offset on both sides of their main steel ratchet ring. But to do that, they pretty much had to reinvent the manufacturing method too.
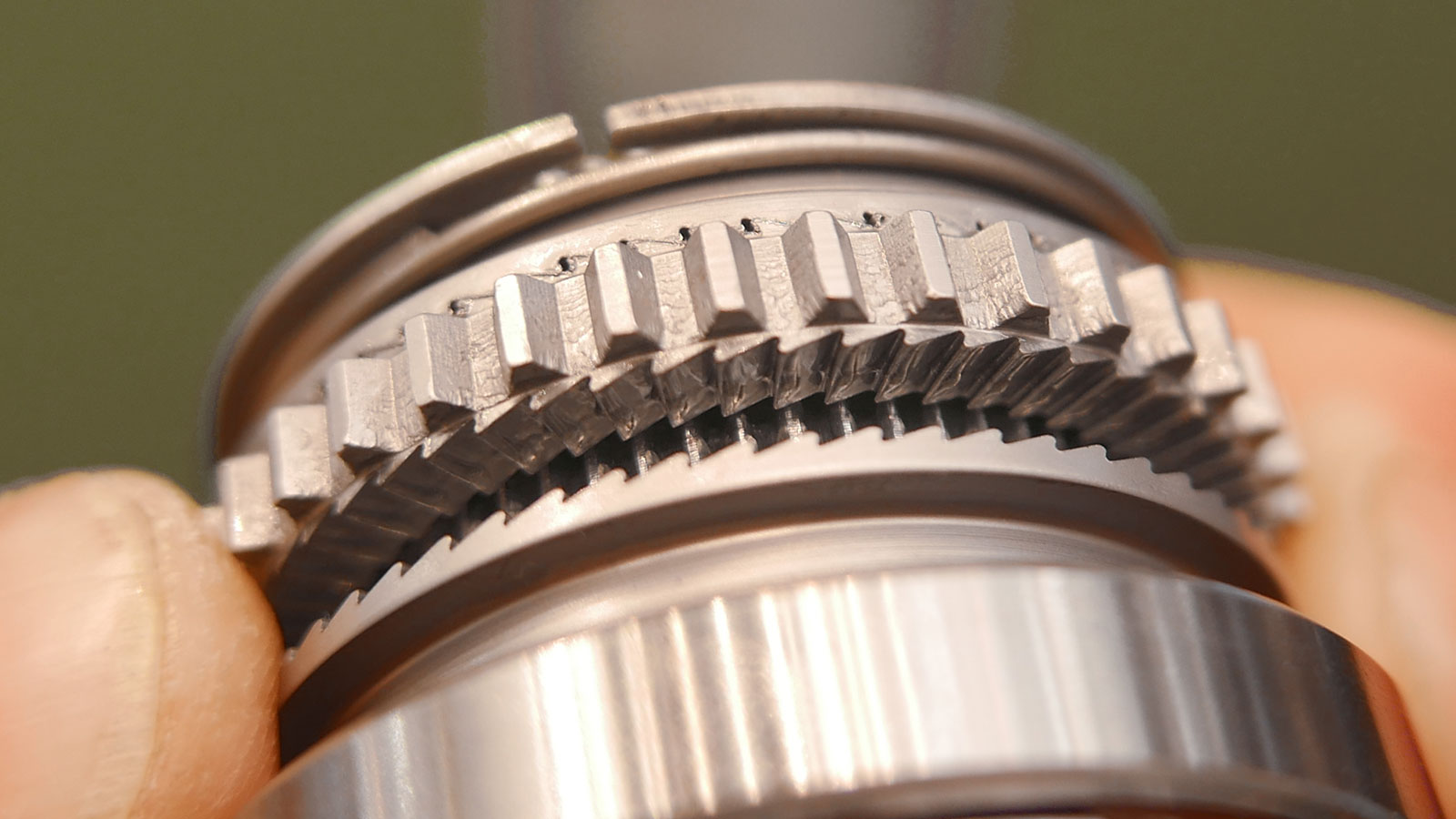
Roman shopped the Qvist idea to existing hub makers. But none seemed set up to run with the new idea.
Then they hunted around for a manufacturing partner. And really, no one could do it for them with the existing machining setups in the bike component sphere.
So Qvist figured out how to design some custom tools to adapt already-established manufacturing techniques. And now are building their hubs and all the key internal elements entirely in-house. That means, they make hubshells, axles, end caps, freehub bodies, and of course those critically unique ratchet rings.
Inside our Qvist Factory Tour: How hubs are made?
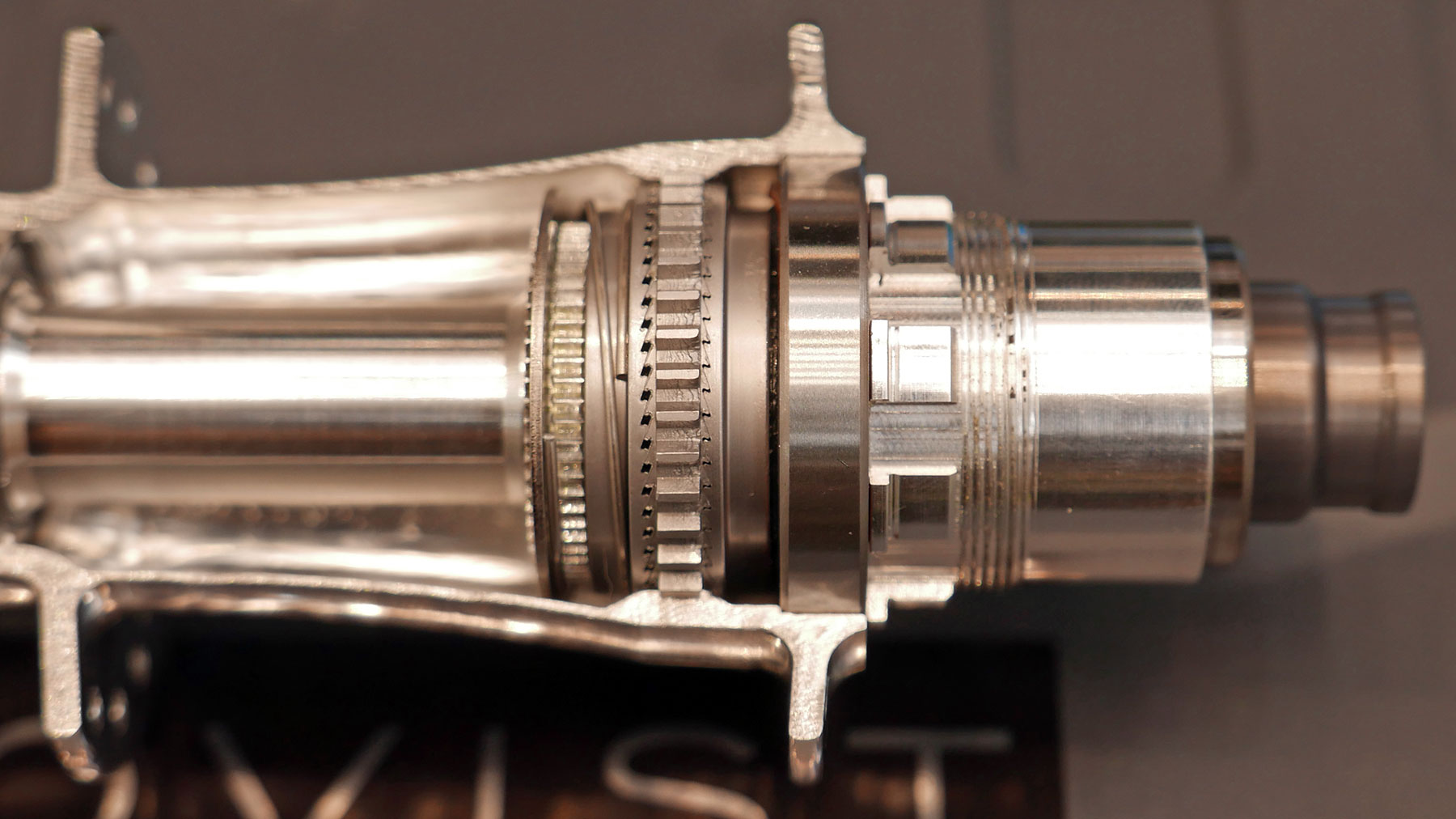
We dropped by the new Qvist manufacturing HQ just outside of Dresden, Germany a few weeks back to see how things were moving ahead on all of the in-house production. The team hadn’t yet gone into full-scale production mode, but had been working through the final setup steps of the more complicated elements.
Qvist’s trick to manufacturing in Germany at competitive (but still premium) pricing has been a lot of automated manufacturing that limits the human labor after setup. All of the hub parts are effectively being machined on three automated CNC machines – a couple of lathes and a more complex mill. Each features unique custom tooling to speed up some machining steps & boost its machine’s capabilities, which we got a sneak peek inside. Plus, automated material feeds and completed parts managers to function autonomously.
Hubshells
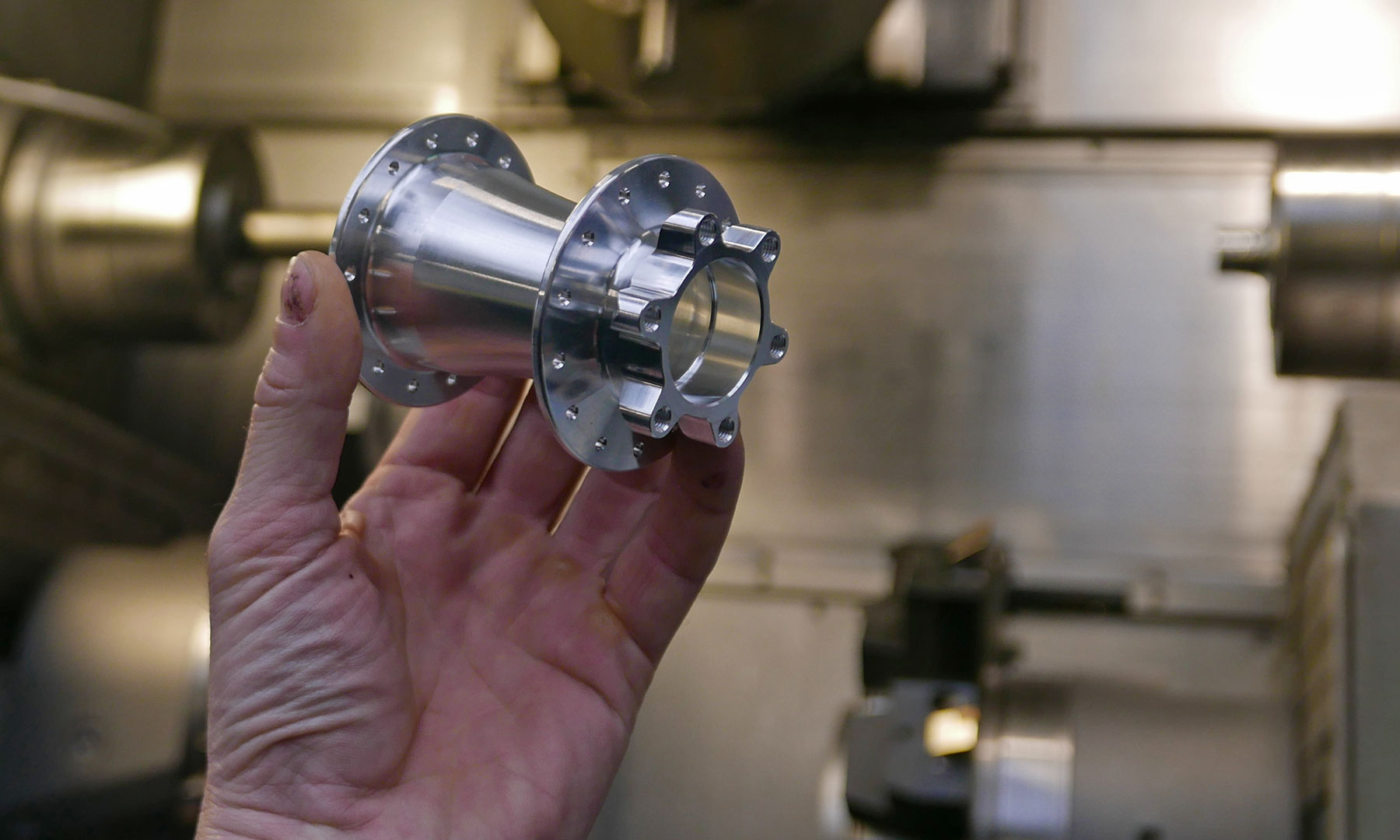
Starting as solid bars of 7075 alloy – like all the other machined aluminum parts – the aluminum hubshells seem simple enough on the outside. But they are not the simplest parts that Qvist makes, and require several machining steps and some creative tooling solutions.
Beyond the 6-bolt rotor interface, threads, and spoke holes, they also get complex inside.
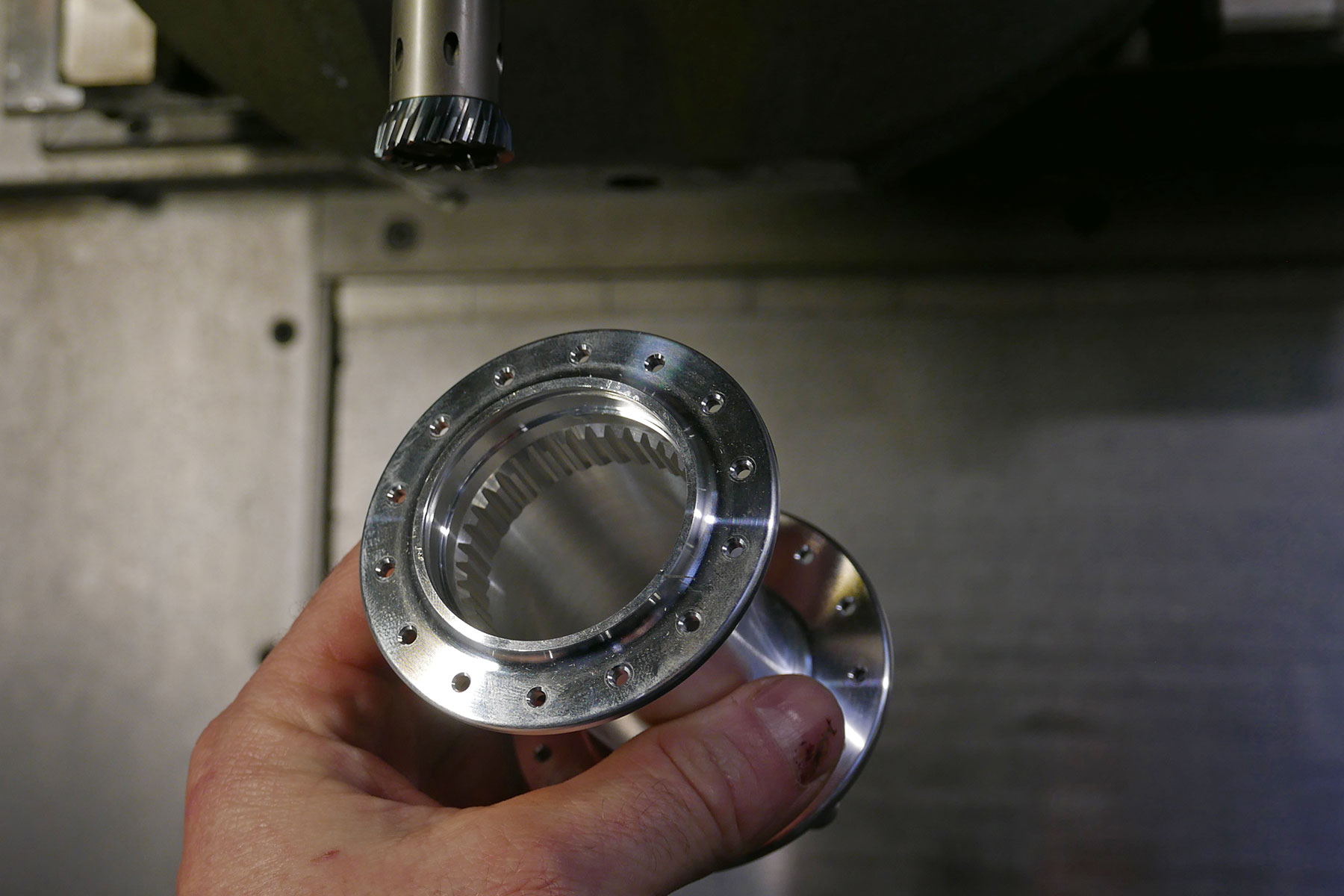
Machined guides inside the hubshell allow the special Qvist Double Ratchet ring to slides back-and-forth inside, alternating between the 2 sets of engagement teeth. But instead of machining each tooth of those guides one-at-a-time, Qvist had this custom tool made that spin in sync with the spinning hubshell of the lathe to quickly cut the straight guides as the hub spins.
It’s the same technique that allows for the creation of all the teeth on the ratchet rings, too.
Freehub bodies
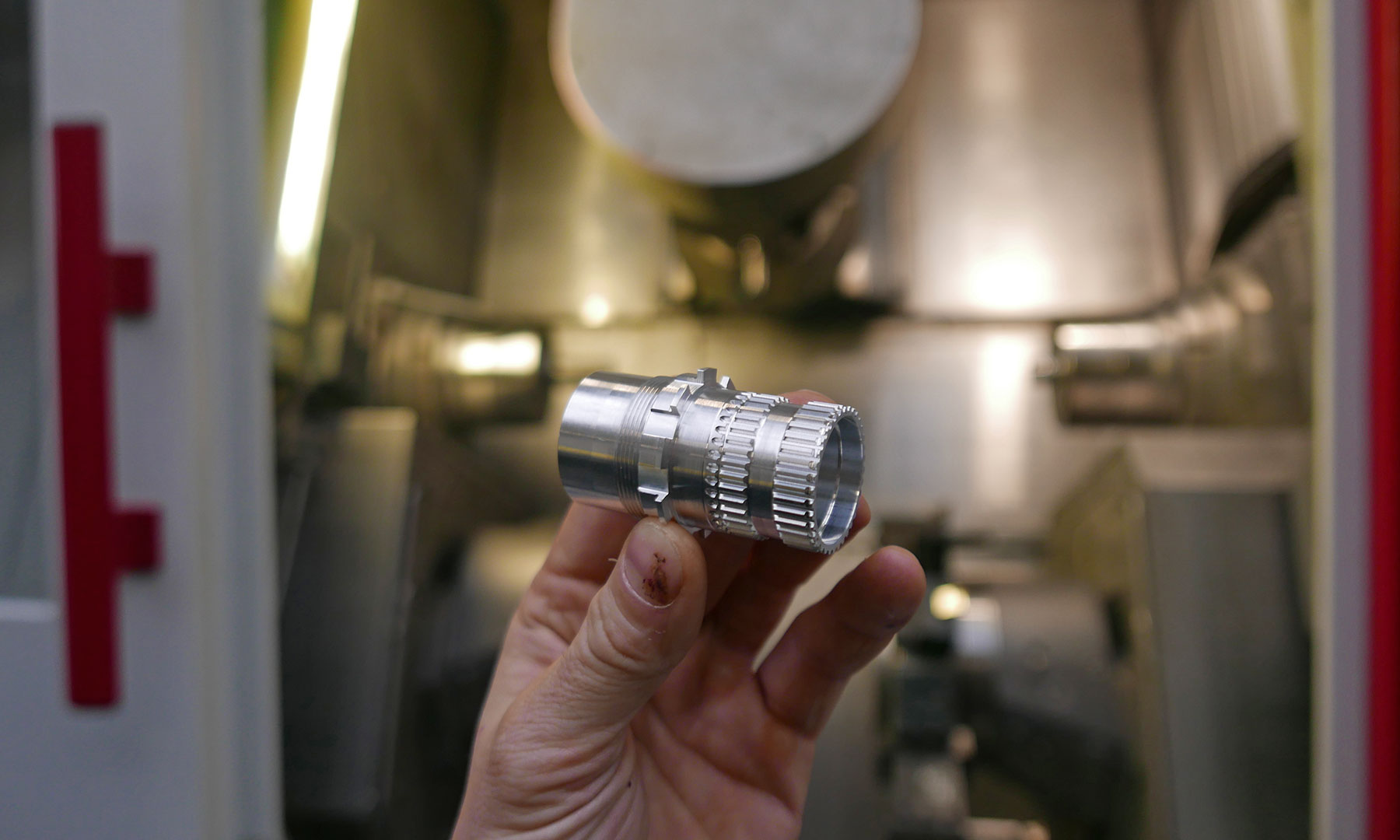
Out of the same multi-head Traub CNC milling machine as the hubshells, comes this freehub body.
That novel Qvist Double Ratchet system also means they need unique and more complex freehub bodies, too. The double-sided ratchet rings engage the guides in the hubshell (while it floats above the smooth section on this freehub body). And on either side a single ratchet ring engages the matching splined guides in this freehub body.
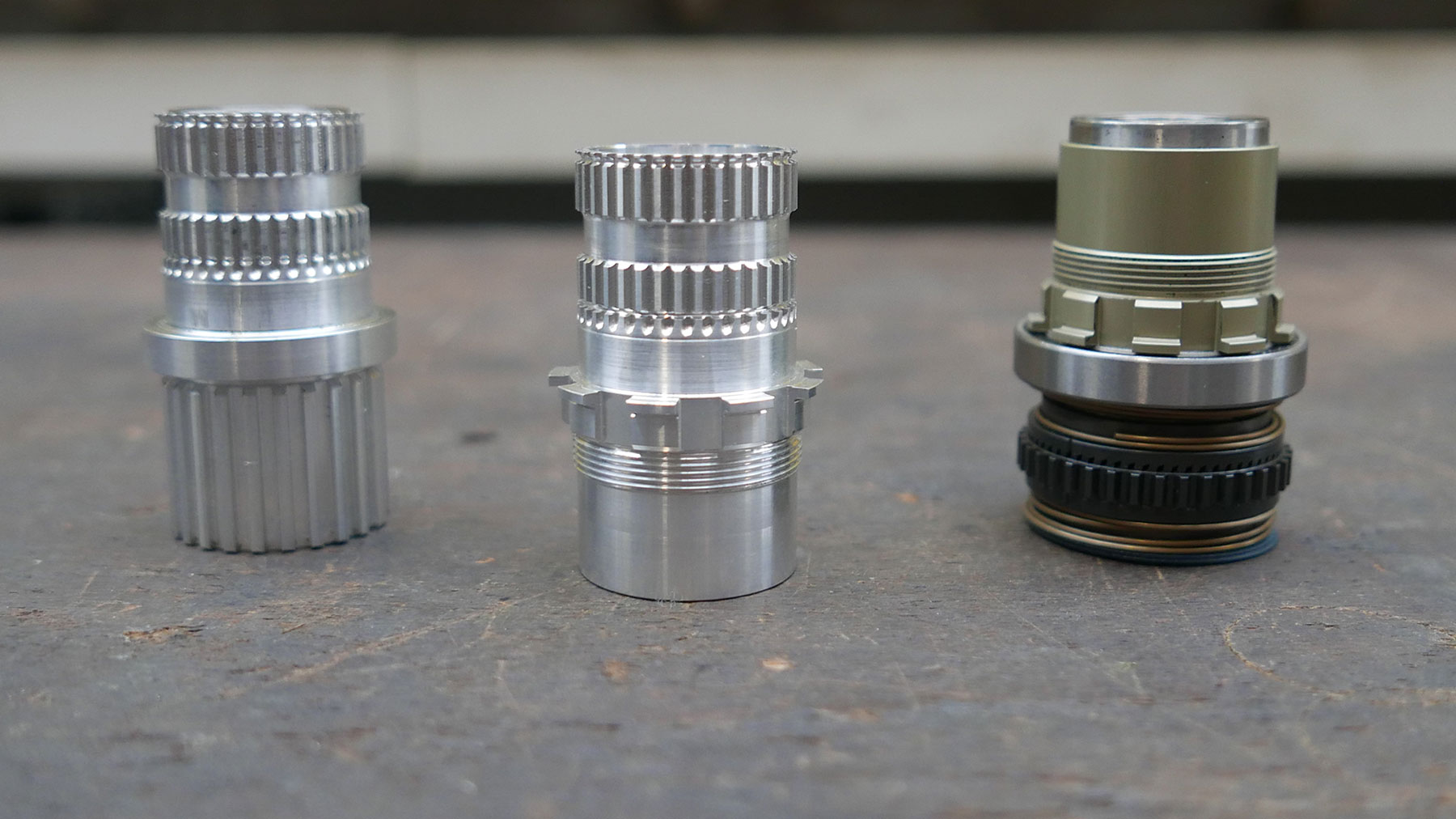
The longer freehubs feature more complicated machining, for sure. And they will certainly be more expensive and more time-consuming to swap vs. the plug-and-play DT Swiss style freehubs. But the ratchet rings, springs, seals & retainer clips will all be easy to swap over whenever a freehub needs to be switched or replaced. But it is a system that is pressed into place, rather than the freehubs that almost fall out of many other ratchet hubs.
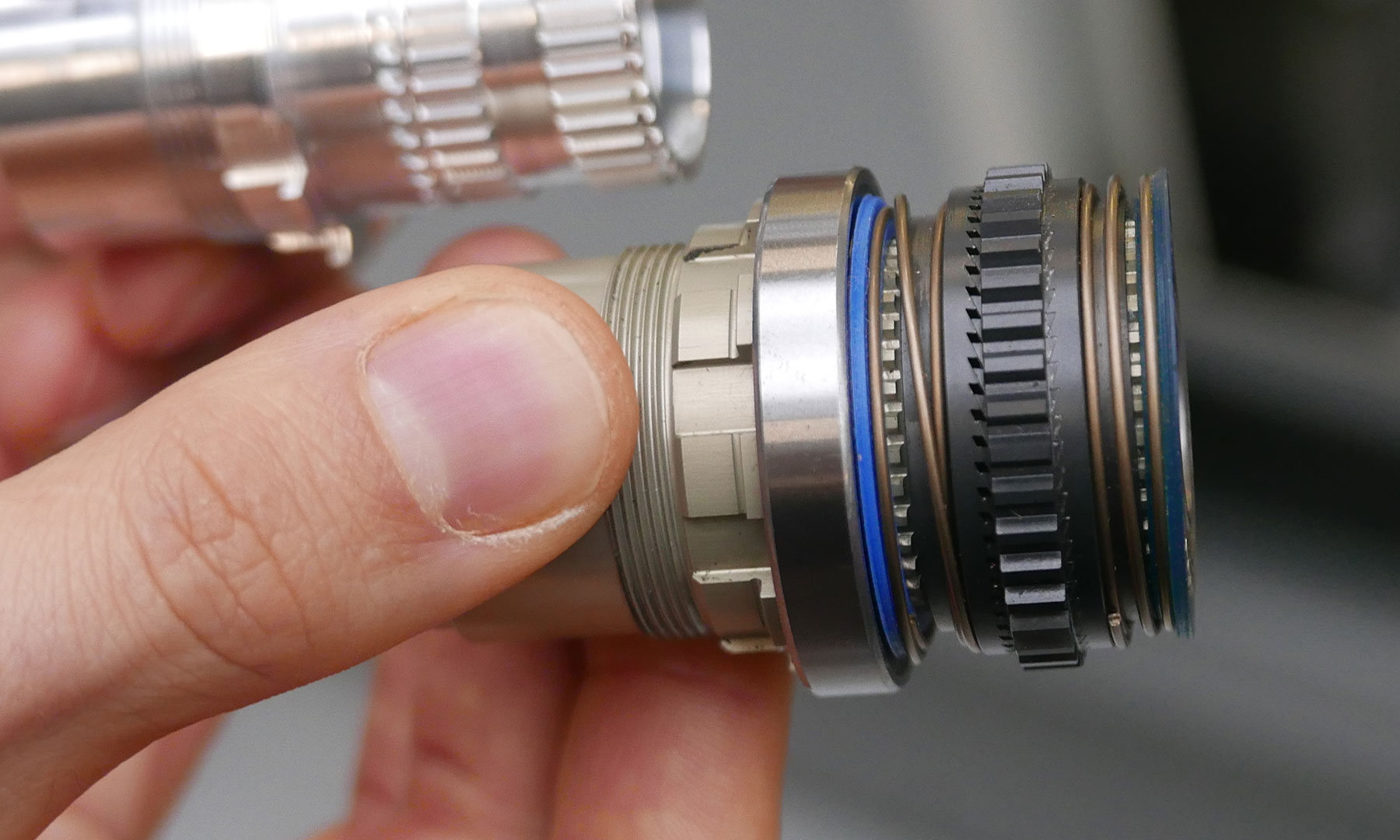
The result of this larger/wider ratchet system though, is that the ratchet actually sits deeper inside the hubshell that a conventional Star Ratchet hub, all inside a larger diameter outer bearing.
That means improved hub stiffness for better wheel strength, longer bearing life, and the ratchets are better protected inside the hub further away from mud/water/dust contamination.
Axles & End Caps
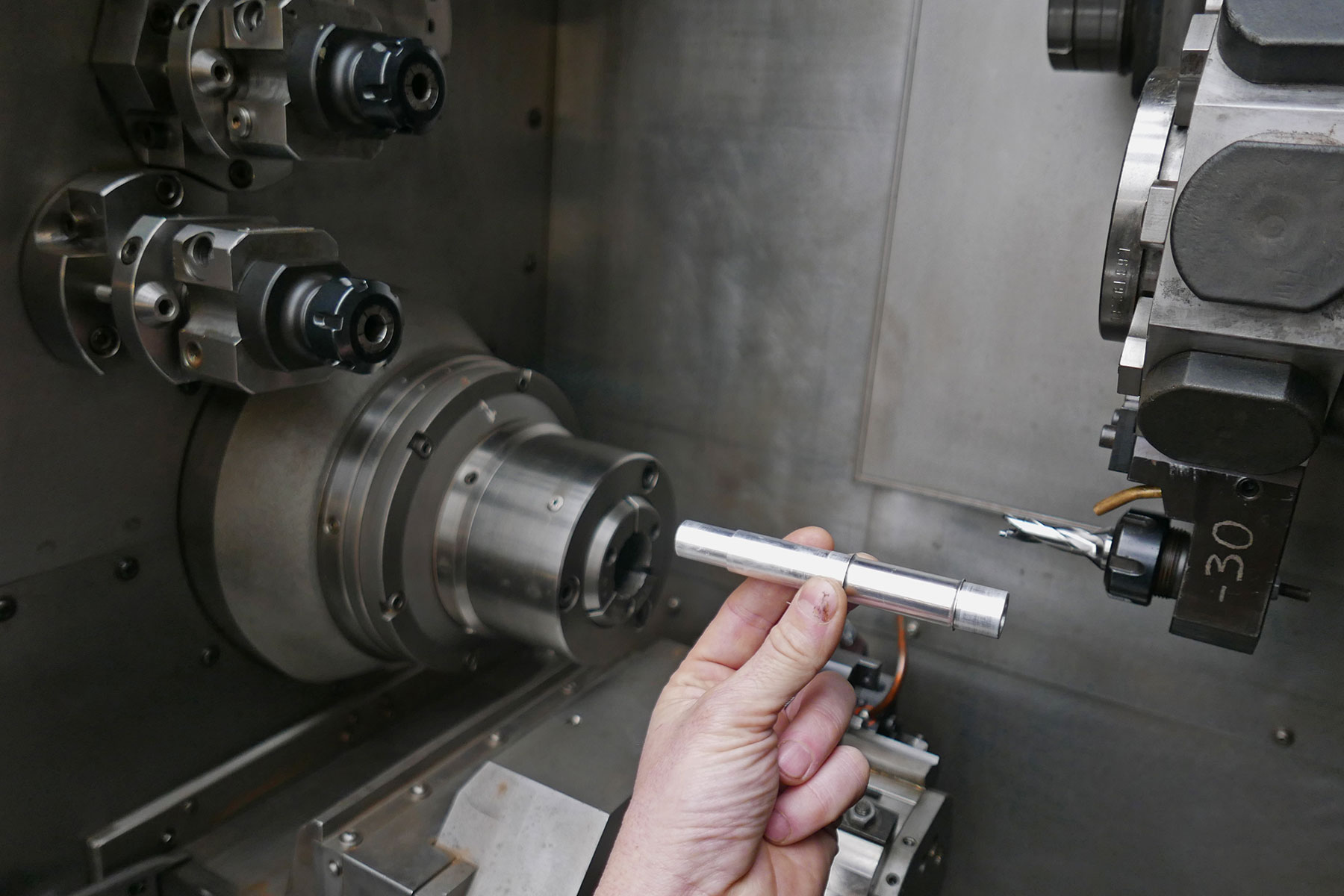
The only thing that genuinely looked simple to manufacture during out factory tour were the aluminum axles and end caps. Yet still, this automated milling lathe seemed up for more complex tasks.
Oversized 17mm axles spin on premium sealed cartridge bearings. Bearings are not made in-house, and ultimately are about the only part of these hubs not made-in Germany, mostly sourced from Japan in standard-sizes that will be easy to replace when they wear out down the road (or trail).
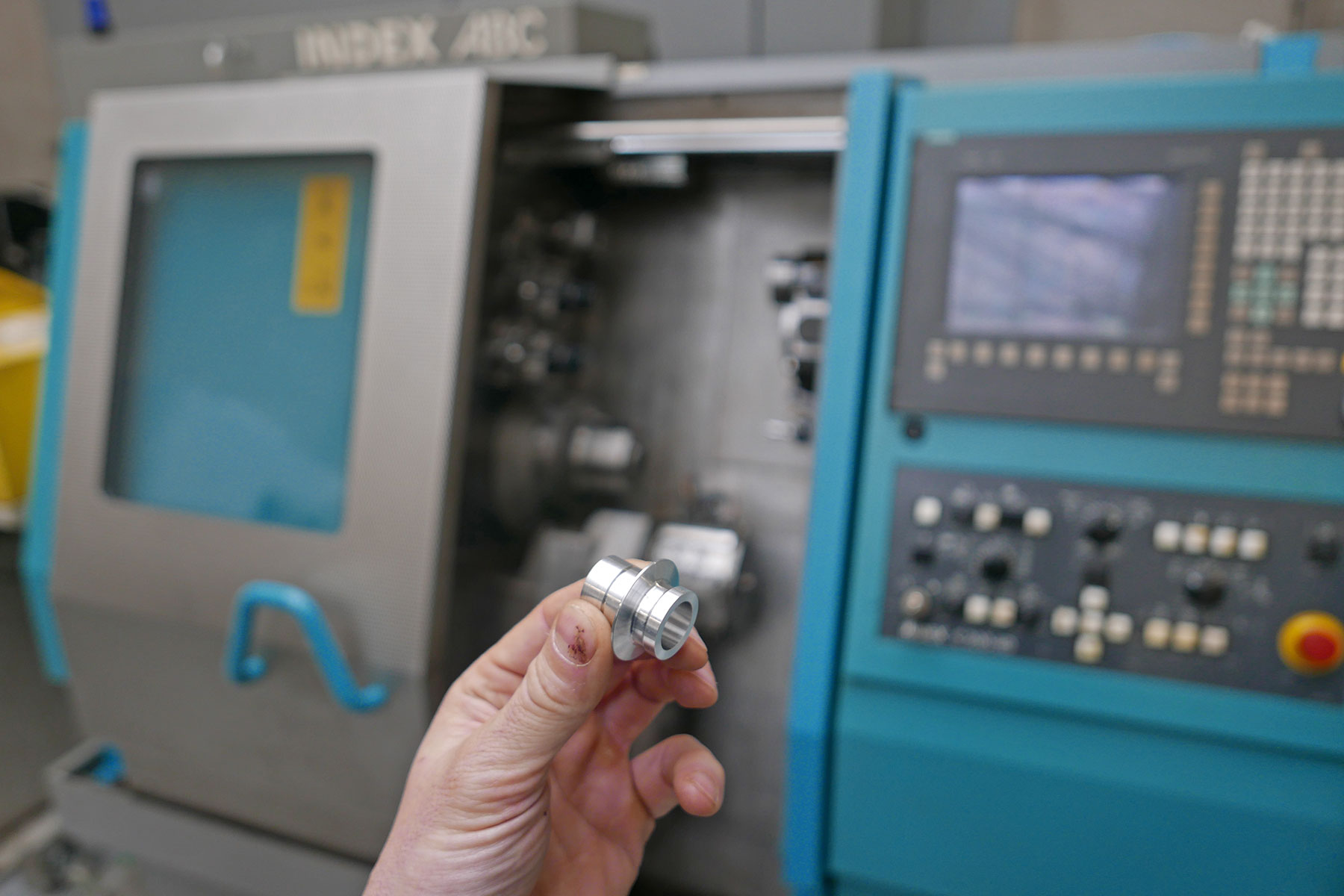
But Qvist did set out to manufacture all of their custom parts in-house, so even these simpler bits get turned on another automated CNC lathe. Various end caps will ensure compatibility with the requisite thru-axle standards, mostly options for their front hubs, including Torque Caps.
The Secret Sauce inside the Qvist Factory
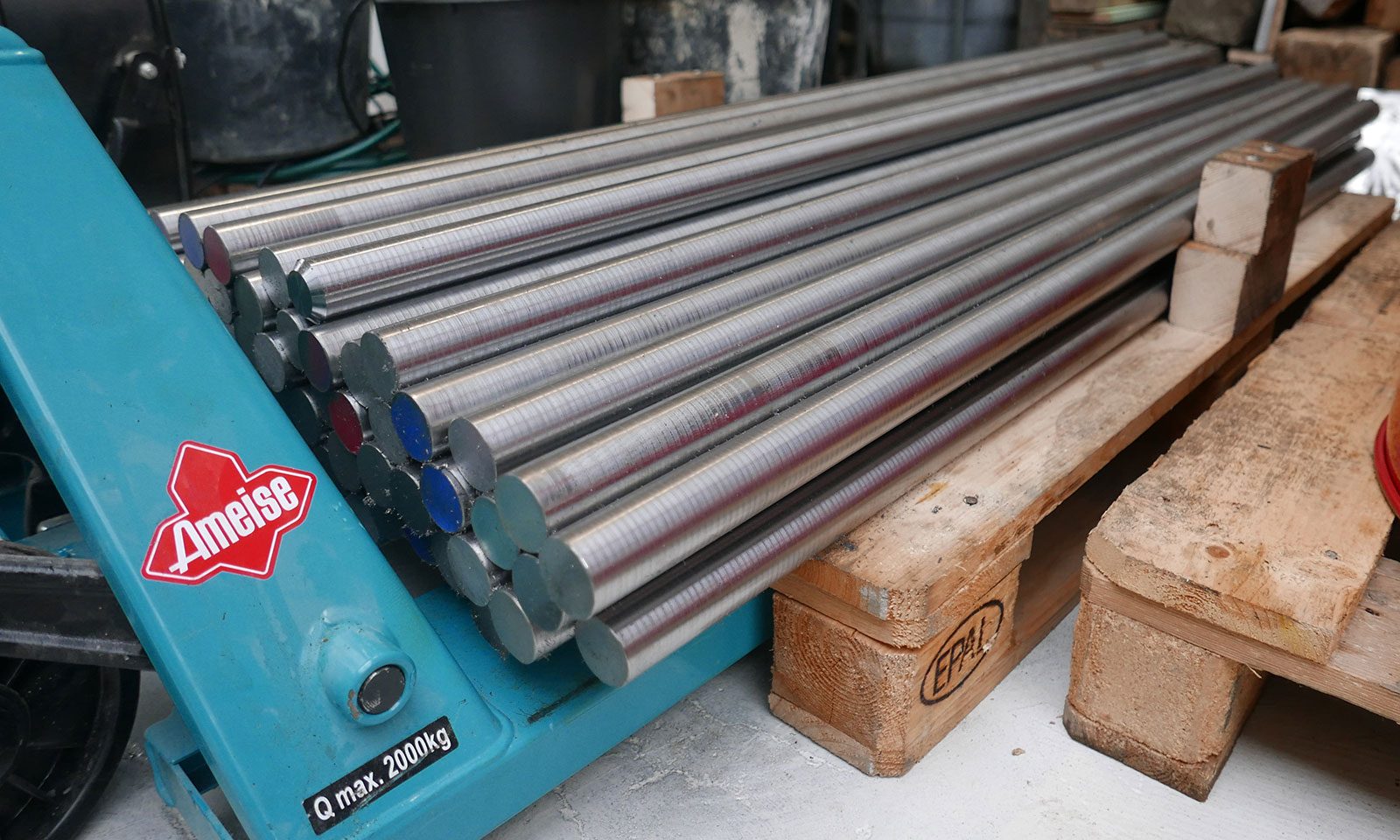
The real heart of the Qvist hub though, are those unique steel double-sided ratchet rings – which all start out as a big long bar of high-strength steel.
Qvist Ratchet Rings
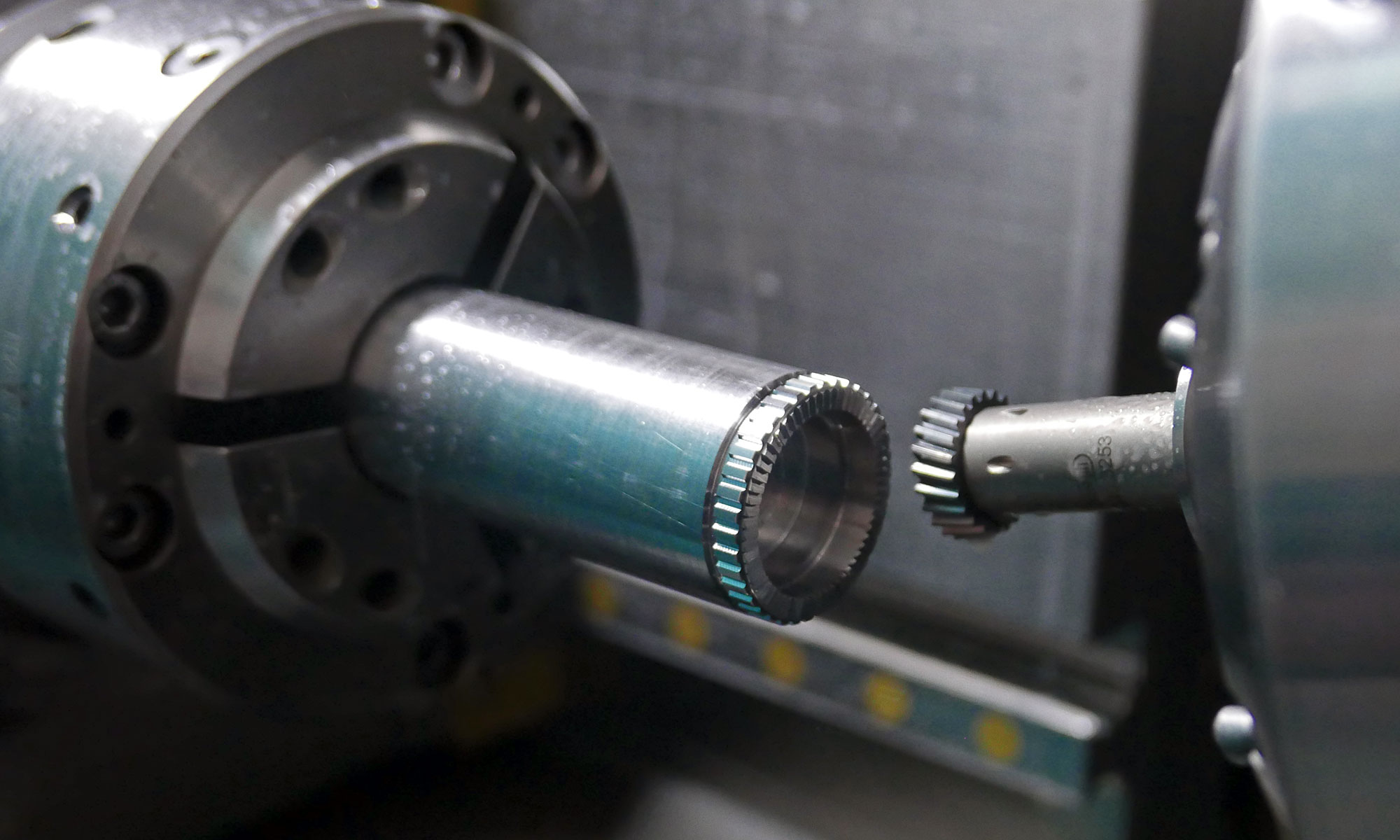
Dropped into the feeder of multi-spindle CNC turn-mill center, bar goes in one end, and little toothed rings come out the other end, after a fully-automated multi-step machining process – inside and out…
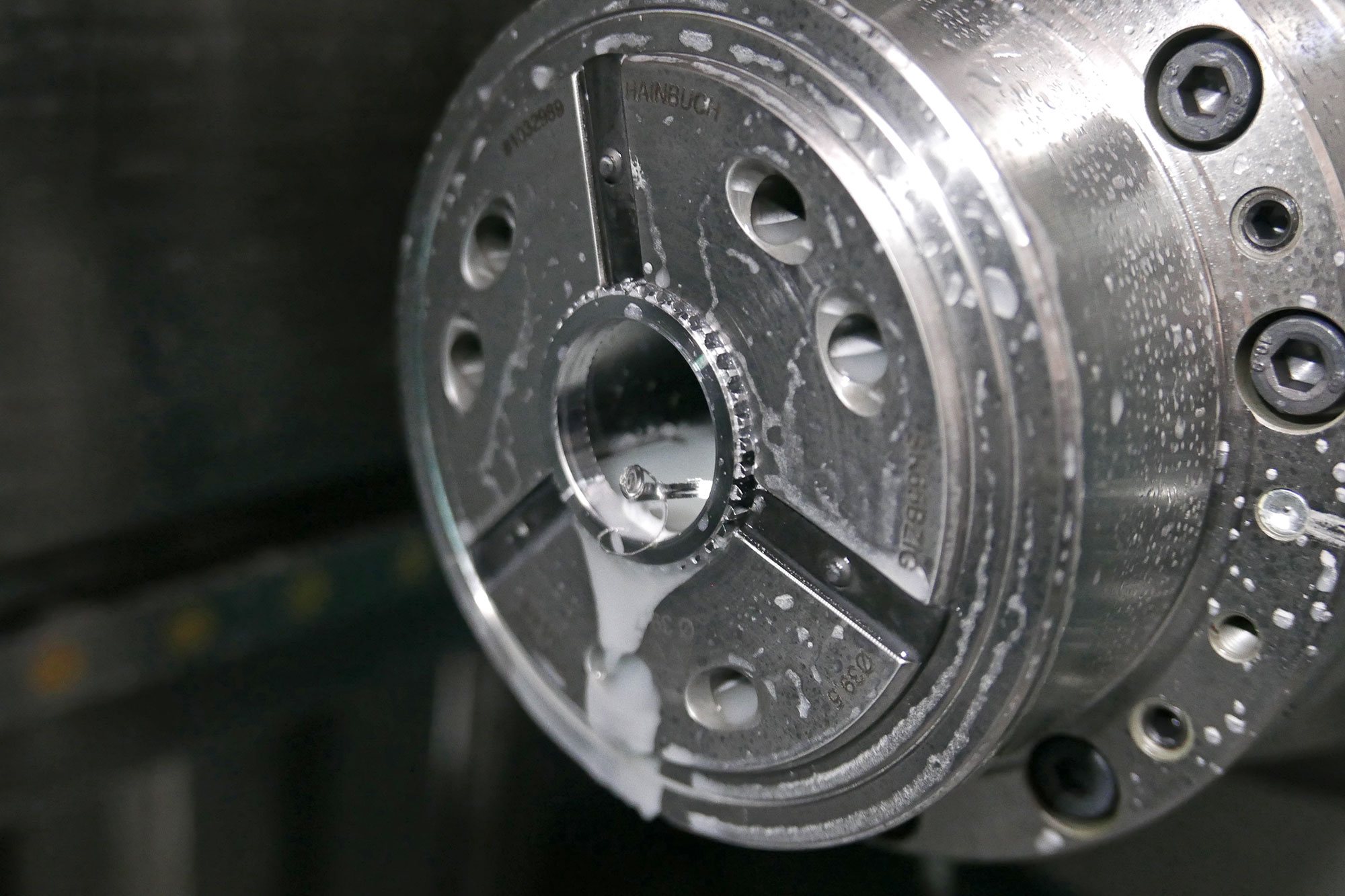
…and then from both ends.
Internal splines, external splines, ratchet teeth – all created with perfectly synchronized skiving. That’s where the material being machined and the tool’s cutting the teeth both spin at the perfectly coordinated correct speed to cut precisely straight teeth across a spinning piece of steel.
Skiving is used for both the double-sided teeth that engage the 2 separate single-sided ratchet rings. And with a separate custom tool for the teeth that guide the Double Ratchet inside the hubshell.
It was pretty cool to watch, even if a bit difficult to get your brain around. Seeing a helical tool spin to cut straight teeth across a counter-rotating rod coming from the other direction.
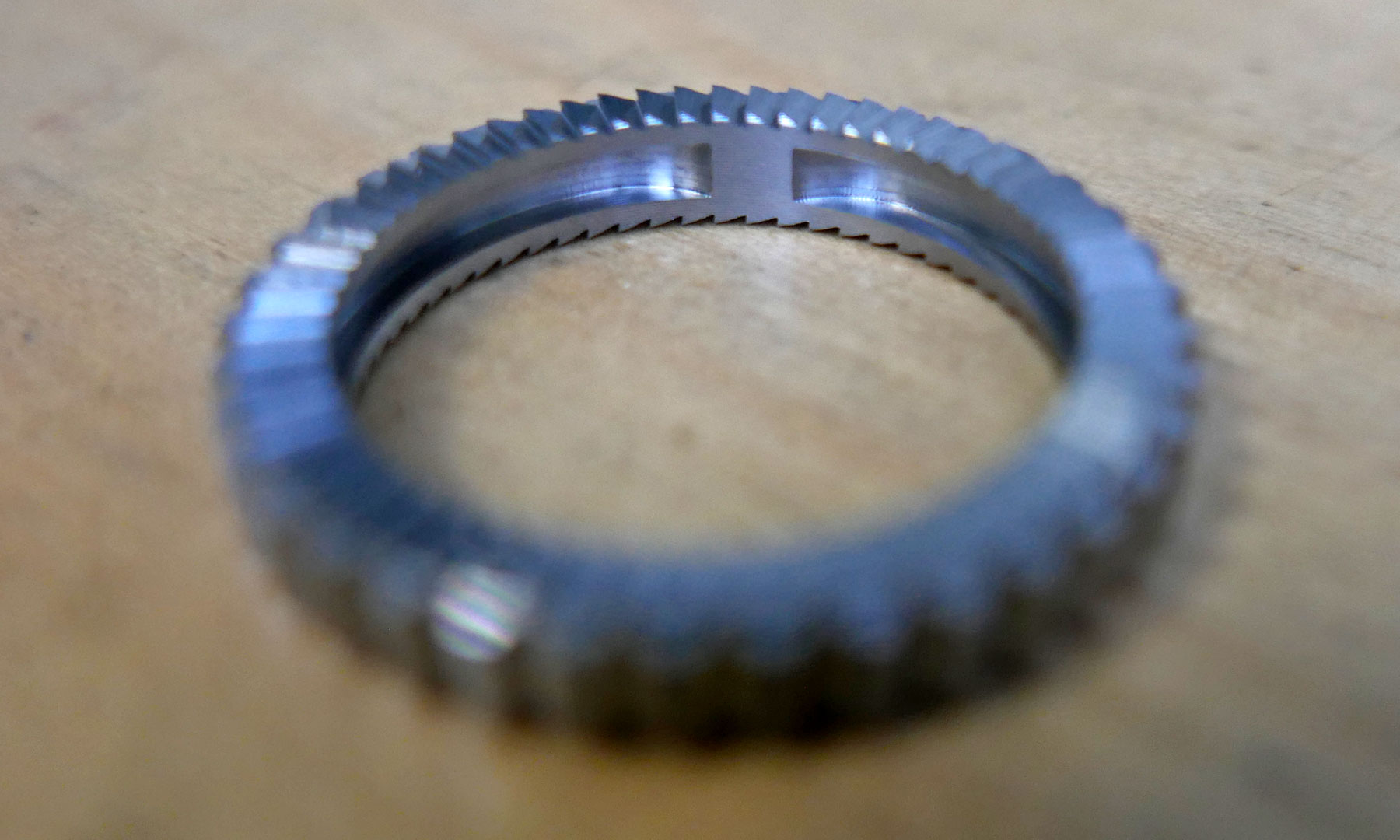
There’s actually a set of 3 ratchet rings, but the center one is the most complex.
Qvist describe the process as old tech. But made much more powerful and precise with the ability of the computing in CNC to perfectly sync the rotational speeds of the tool spindle and the component spindle.
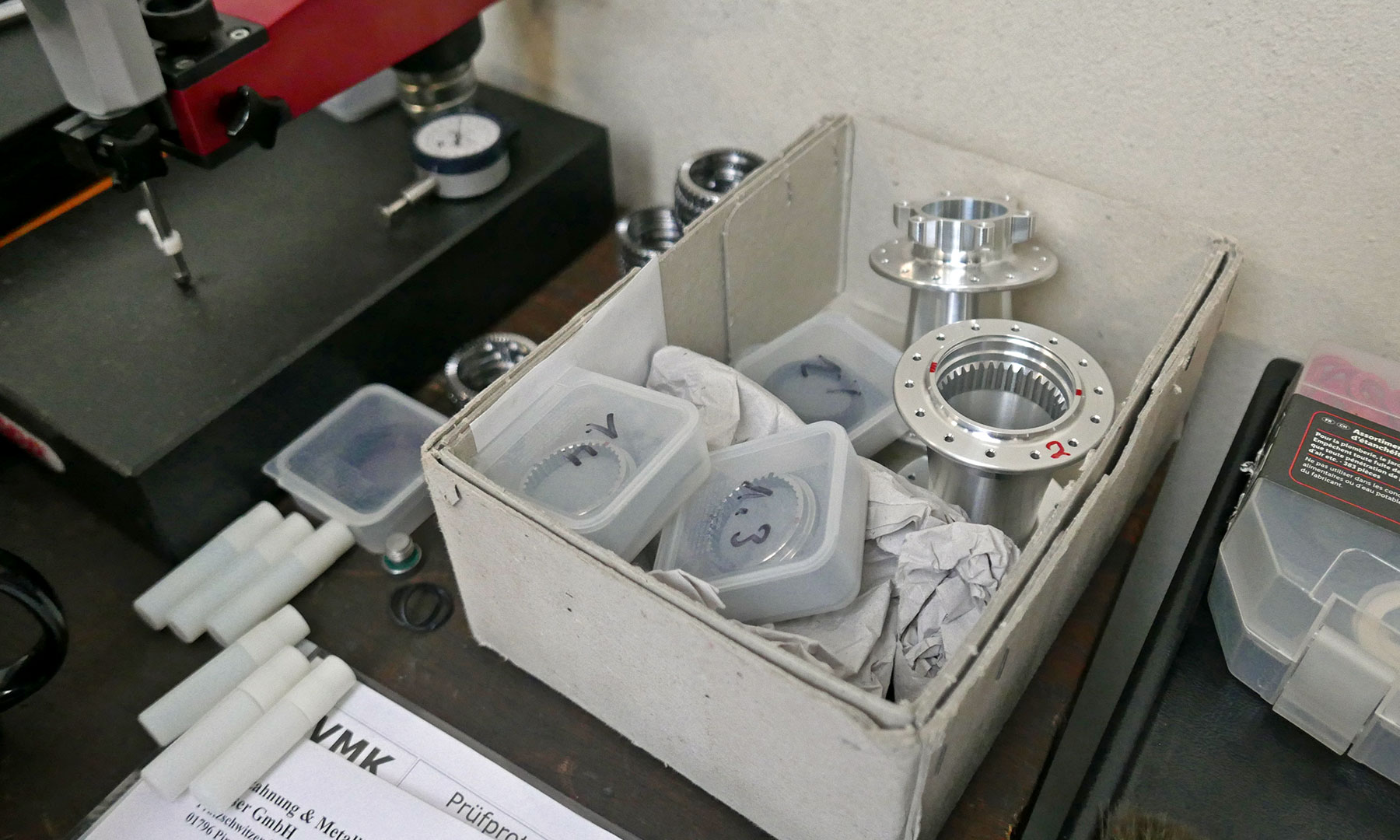
Initial prototyping and first quality control is all done in house. But Qvist outsources production quality control to local testing labs who specialize in ensuring the highest standards are met.
Another key interesting bit, the whole thing happens in a bath of plant-based and biodegradable cutting fluid. But not in conventional oil. The whole Qvist manufacturing workshop smelled surprisingly clean. And not as greasy as you normally would sense in a machine shop. Roman says that came down to the fact that they just wanted to create a more healthy environment if they were going to be working there every day. It’s maybe marginally less efficient than conventional cutting oil. But cleanup is so much easier, as is separating the machined material scrap that gets sent back for recycling.
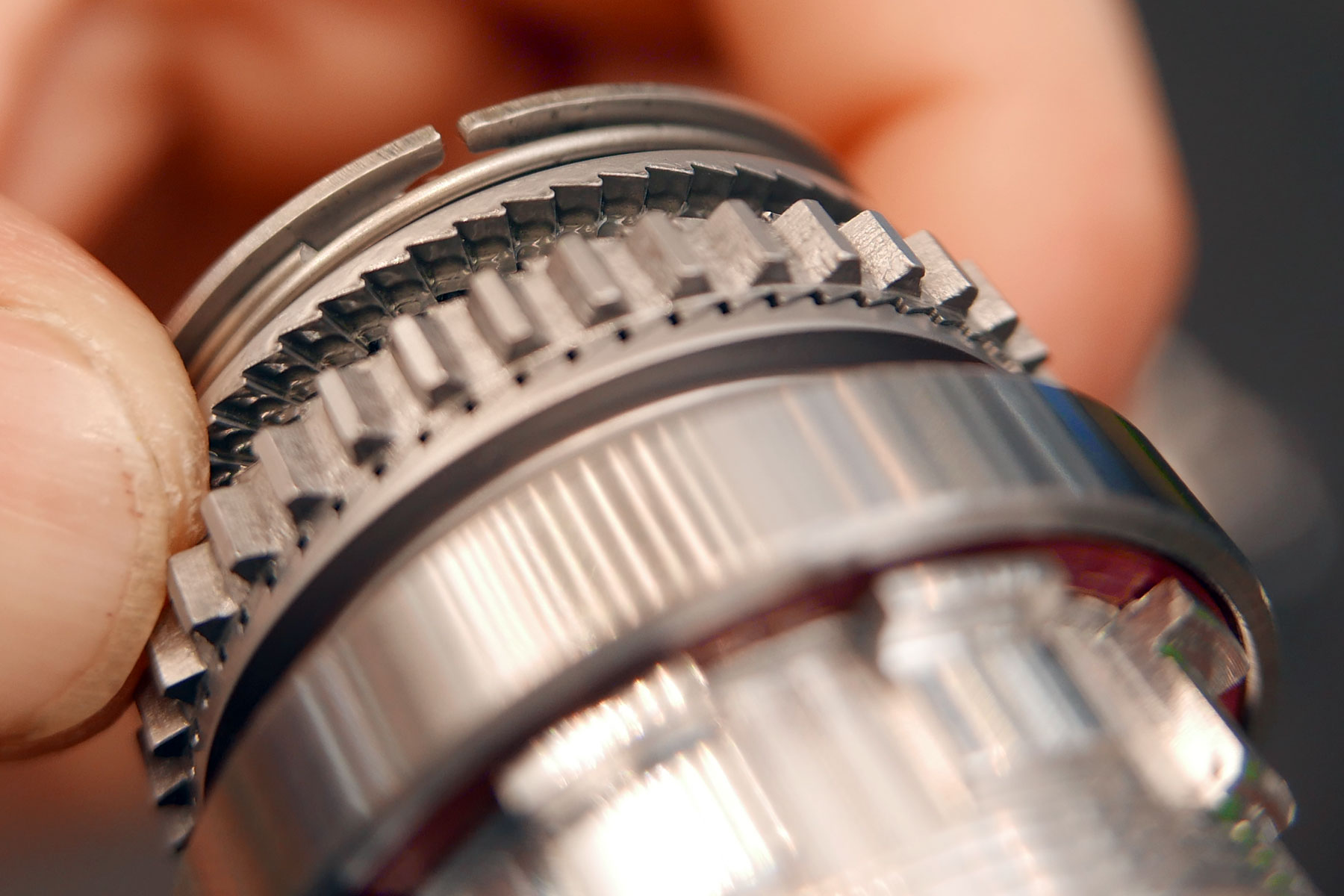
In the end, this final production Qvist hub boasts 120 total teeth – 60 on each side – for a quick 3° engagement angle. That makes it one of the fastest engaging road or mountain bike hub on the market. All with classic ratchet hub security.
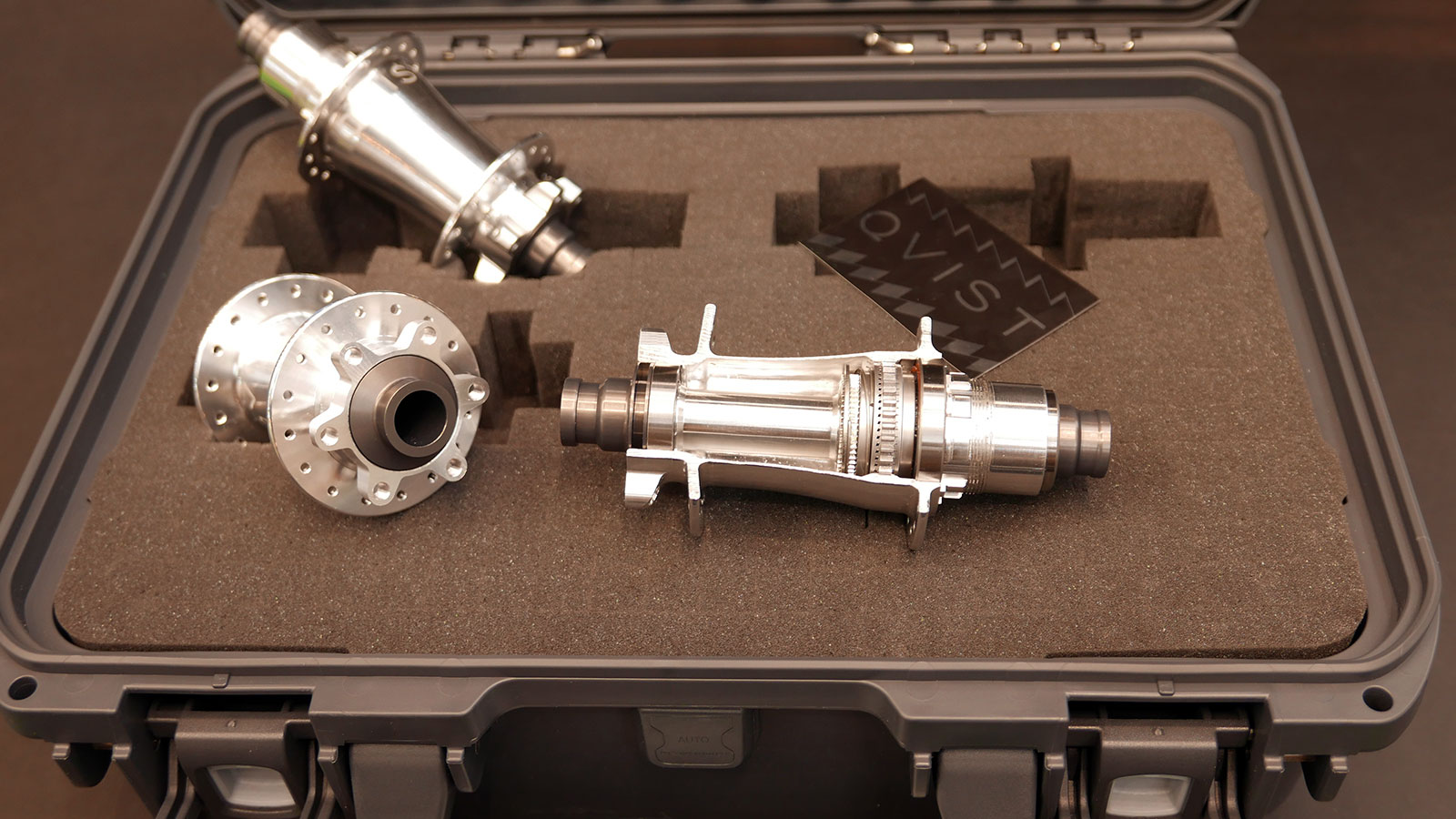
Qvist hubs & wheels – Pricing, Options, Pre-sale Discounting & Availability
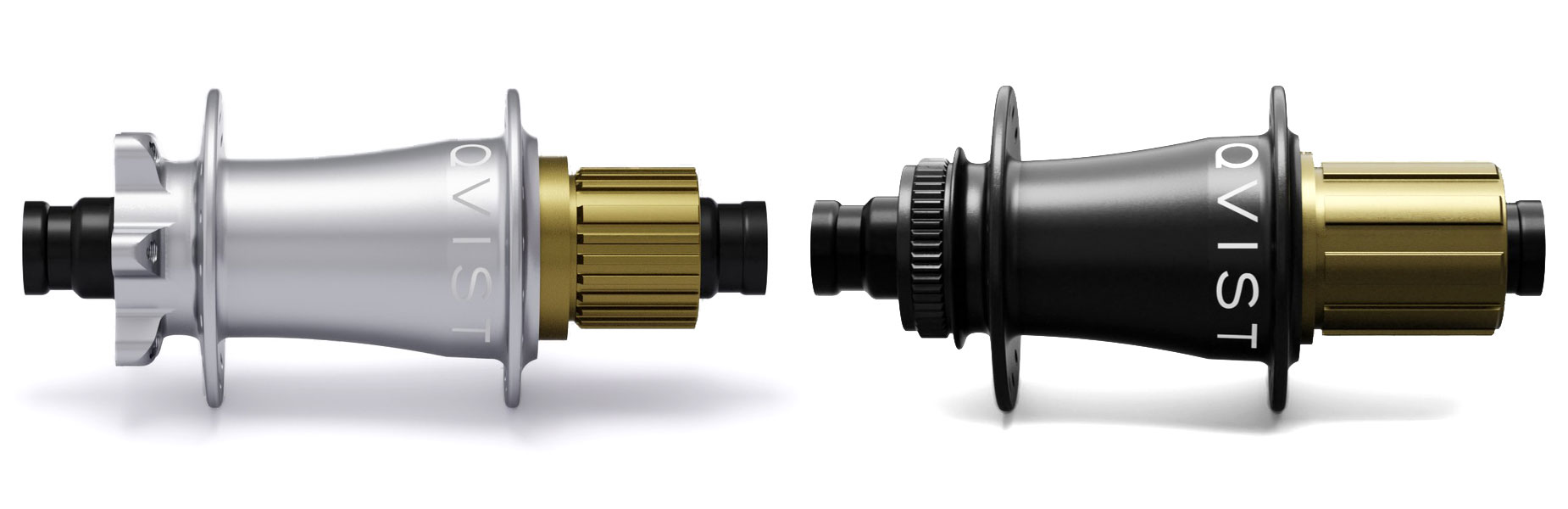
The finished Qvist hubs with all that lovely in-house manufactured tech inside are now available for pre-order. You get to pick from a number of core options, with rear hubs retailing for 500€. Boost rear mountain bike hubs (from 290g, claimed) are 6-bolt, come in 28 or 32 hole drilling. And in silver or black ano. Then, pick from Shimano HG, MicroSpline, or SRAM XD freehubs. Non-Boost rear road/gravel/cx hubs (265g) are centerlock in 24,28, or 32H drilling. Again, silver or black with HG, MicroSpline, or XDR freehubs.
A Superboost hub and a Single Speed hub designed for modern gearbox bikes are both in the works, as well.
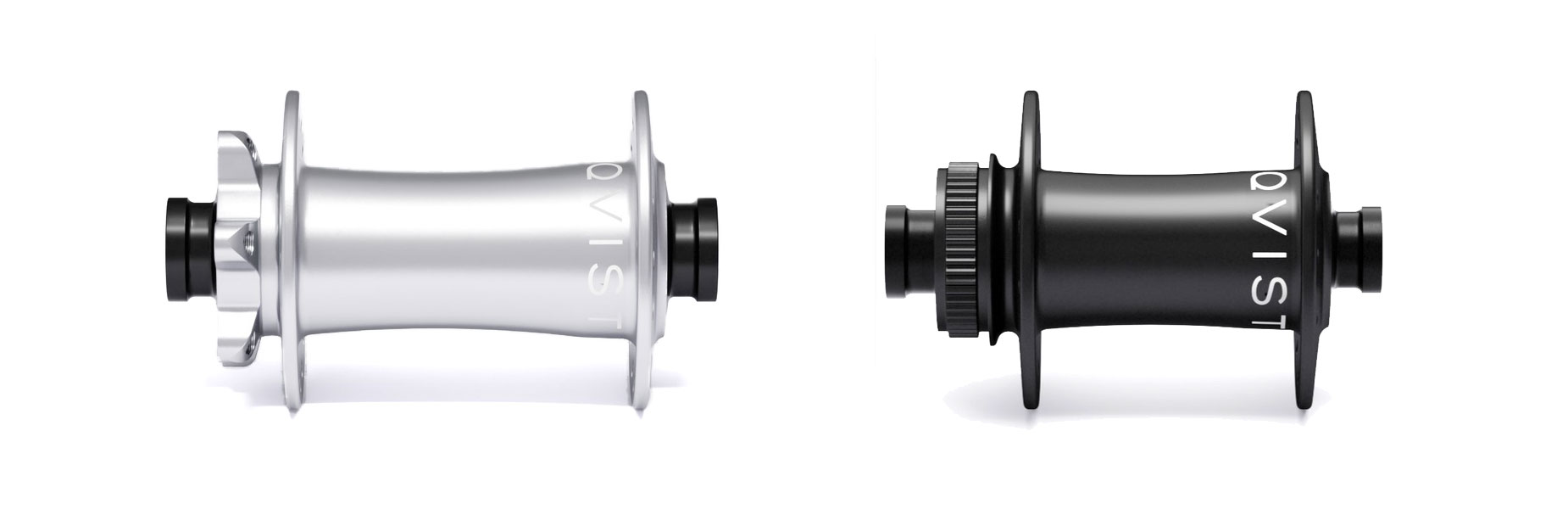
Qvist also machines matching front hubs in house for 200€ a piece. Boost 6-bolt hubs (160g) can pick 12mm, 15mm, 20mm or RockShox-friendly Torque Cap thru-axle end caps & 28/32H drilling. Non-Boost centerlock hubs (120g) pick 12 or 15mm end caps & 24/28/32H drilling. Either in silver or black.
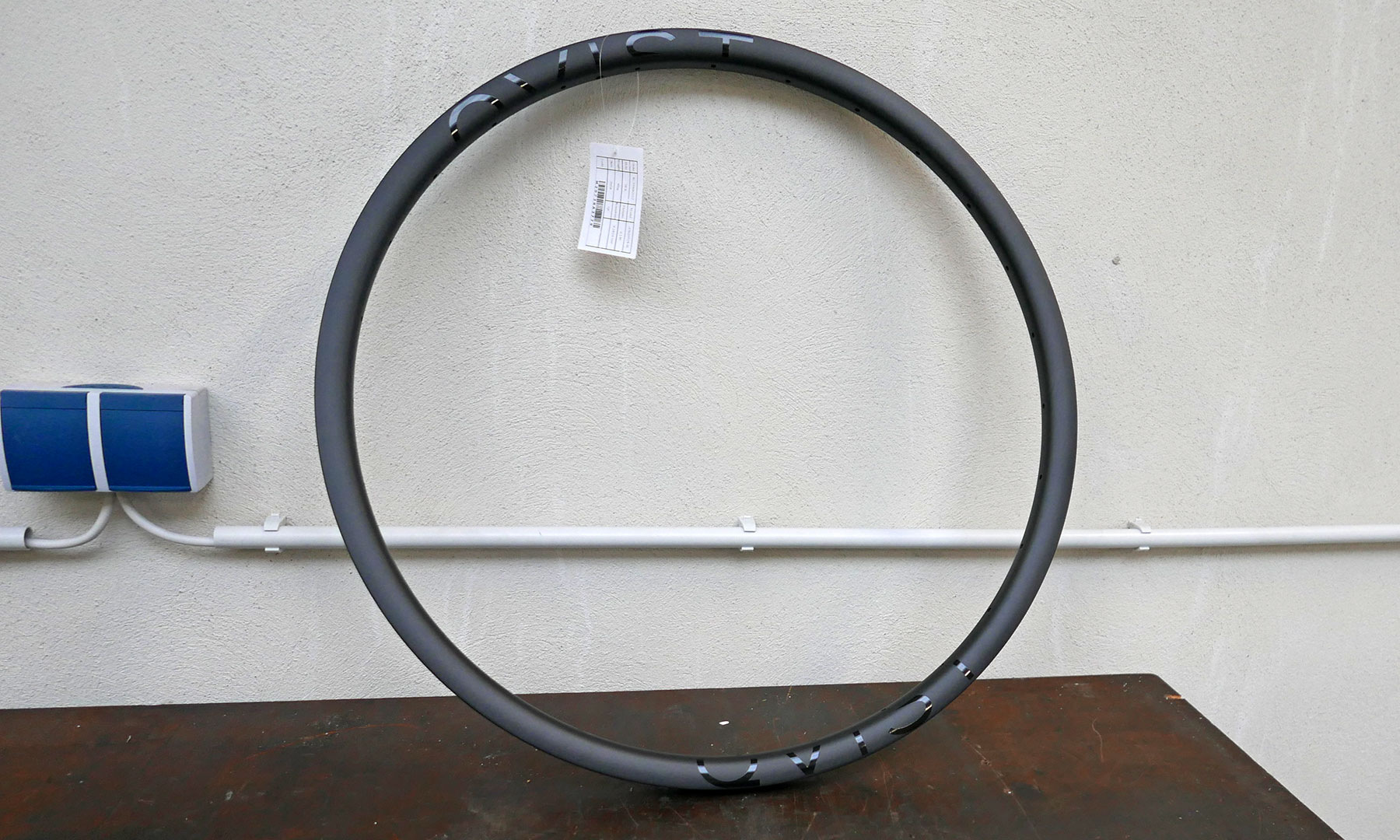
On top of hubs, Qvist understands a lot of cyclists just want a complete set of wheels to ride out of the box. So they sourced their own carbon & alloy rims. And they will custom build up road, gravel, XC, trail, or enduro wheels too in house in Germany. There are tons of options to choose from, all laced with Pillar spokes. Admittedly, Qvist sources alloy rims in Taiwan, and carbon rims in China. Apparently Qvist tested a bunch of options. And the Chinese carbon option delivered by far the best quality. Qvist are still working on a EU-made carbon option in the future too, though.
There really are too many options to get into detail: 18.5-26mm deep x 27-30mm internal for MTB. 25-50mm deep x 21-27mm wide internal for road & gravel. The Qvist carbon rims are even available separately for 400€ a piece if you want to build your own wheels.
What’s next for Qvist?
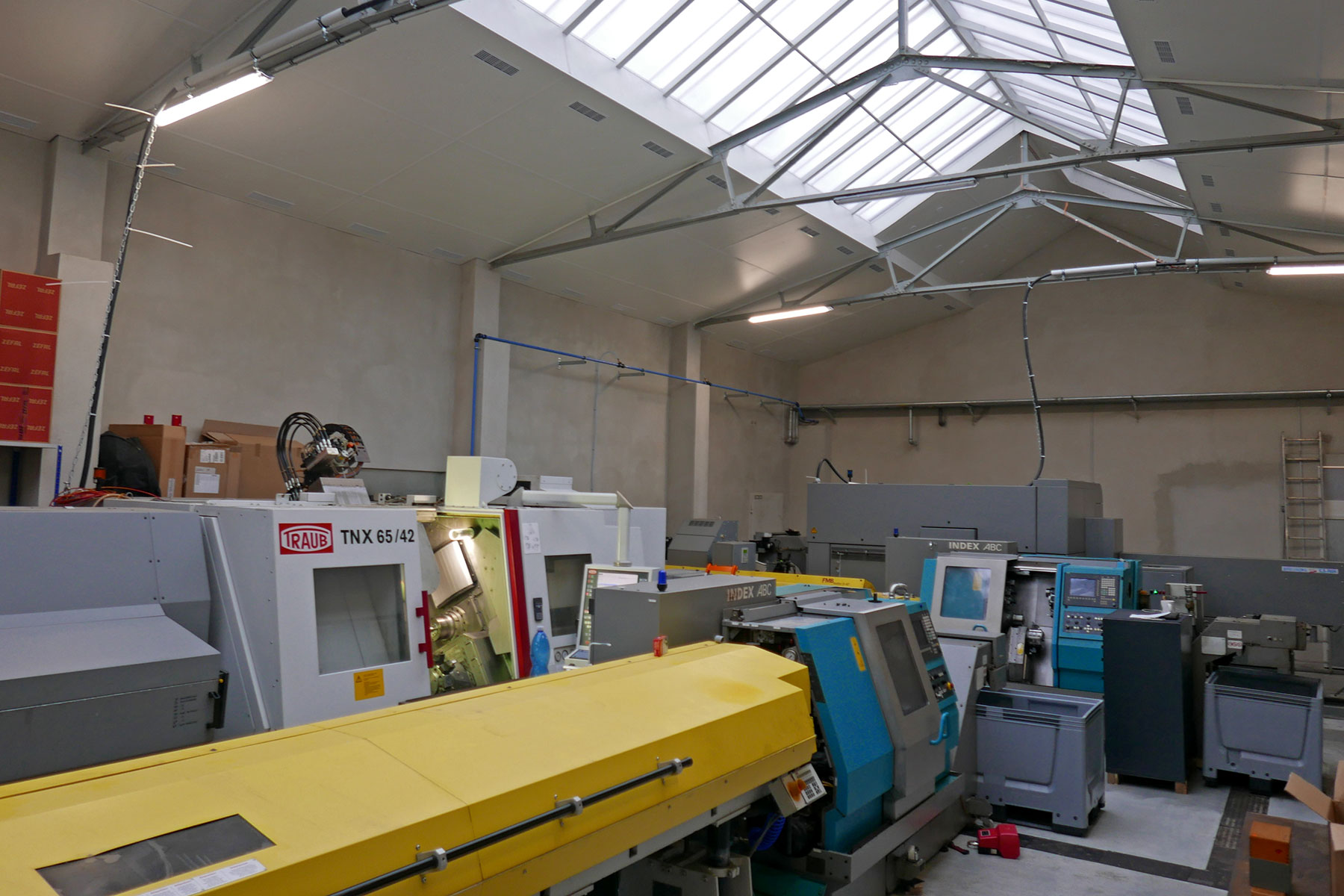
Qvist are a completely new component maker with a lot of great ideas, plenty of engineering experience, solid manufacturing expertise, and a solid position in the Saxony bike manufacturing community. As we visited them in mid-December, Qvist are still in the process of ramping up production. Yet they seem to have dialed-in their unique machining processes. Even if some of the automated material handling setups weren’t quite finished yet.
It also looks like they’ve drummed up a lot of interest with the truly unique Double Ratchet hub, over the last 18 months. So I suspect they’ll be working hard to meet initial production hub demand.
But their product development team isn’t sitting still. In fact, they’ve also got a 4th fancy (& expensive) CNC machine – another lathe sitting in the workshop waiting to start producing headsets and bottom bracket cups. There’s no word on pricing, options, or availability yet. But as soon as they dial-in hub component automation, we expect to see more components getting cranked out of the Qvist workshop – just outside of Dresden, Germany.
Pre-order Discount Now
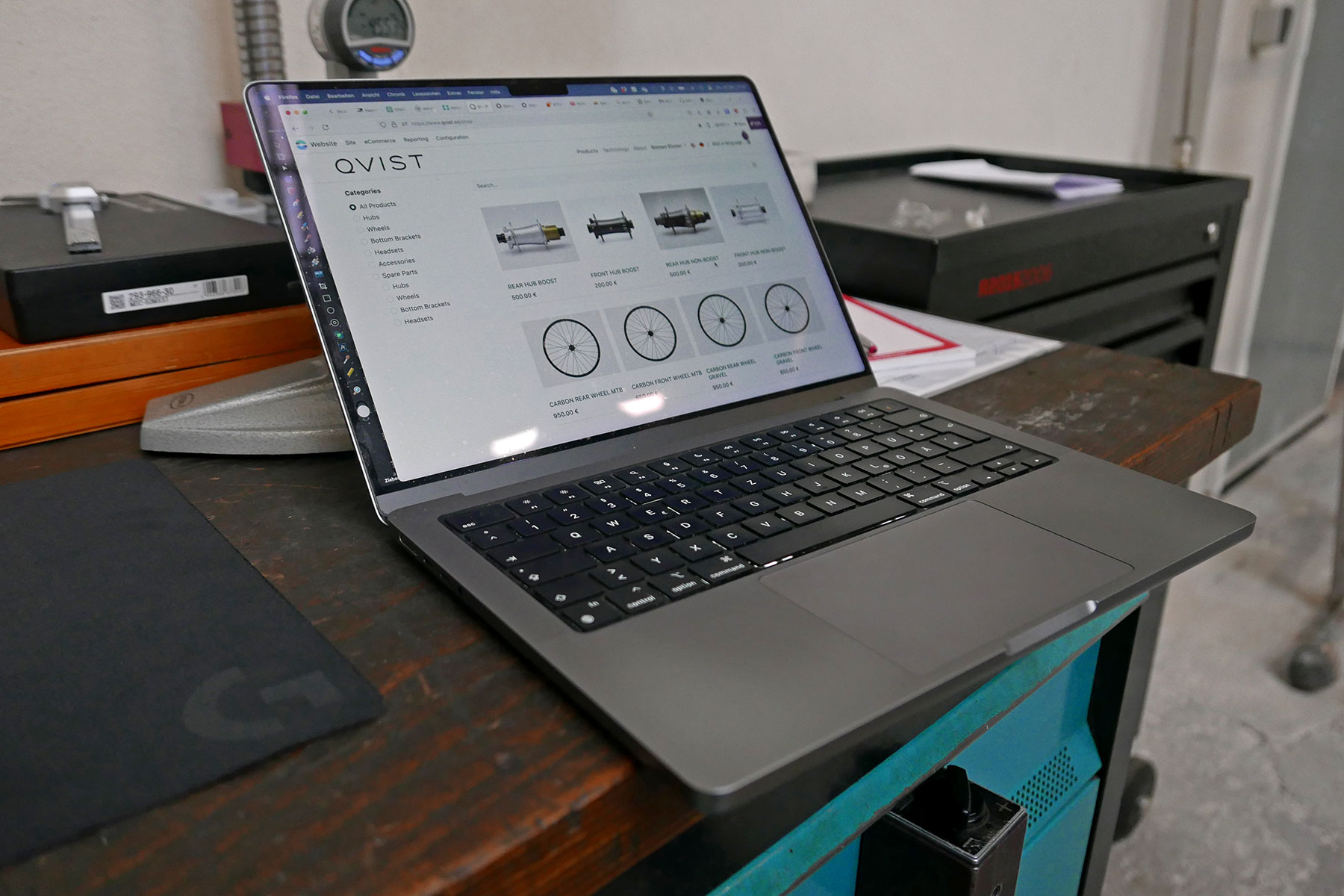
All of the new hubs, rims, and wheels are available to pre-order now direct from Qvist. Deliveries scheduled to start shipping at the end of February and into March 2024.
Shop now direct from Qvist’s online shop for any combo of their new components. And save 10% off retail pricing though the end of this month, January 2024. Use code: PRESALE at checkout to save.