Since our first visit to Allied Cycle Works’ original factory in Little Rock, a lot has changed. They moved near Bentonville, giving them access to way more trails, and their process has been continually refined as they’ve added new models. The latest is the BC40 XC mountain bike, named for the massive Back Forty trail network there.
In this factory tour, Allied’s sales manager Will walks us through how they make their frames, including the linkage parts for the MTB, and how that differs from their road bikes. Check the video for the full story, and scroll down for more detailed photos and notes.
Allied Cycle Works Factory Tour Photos
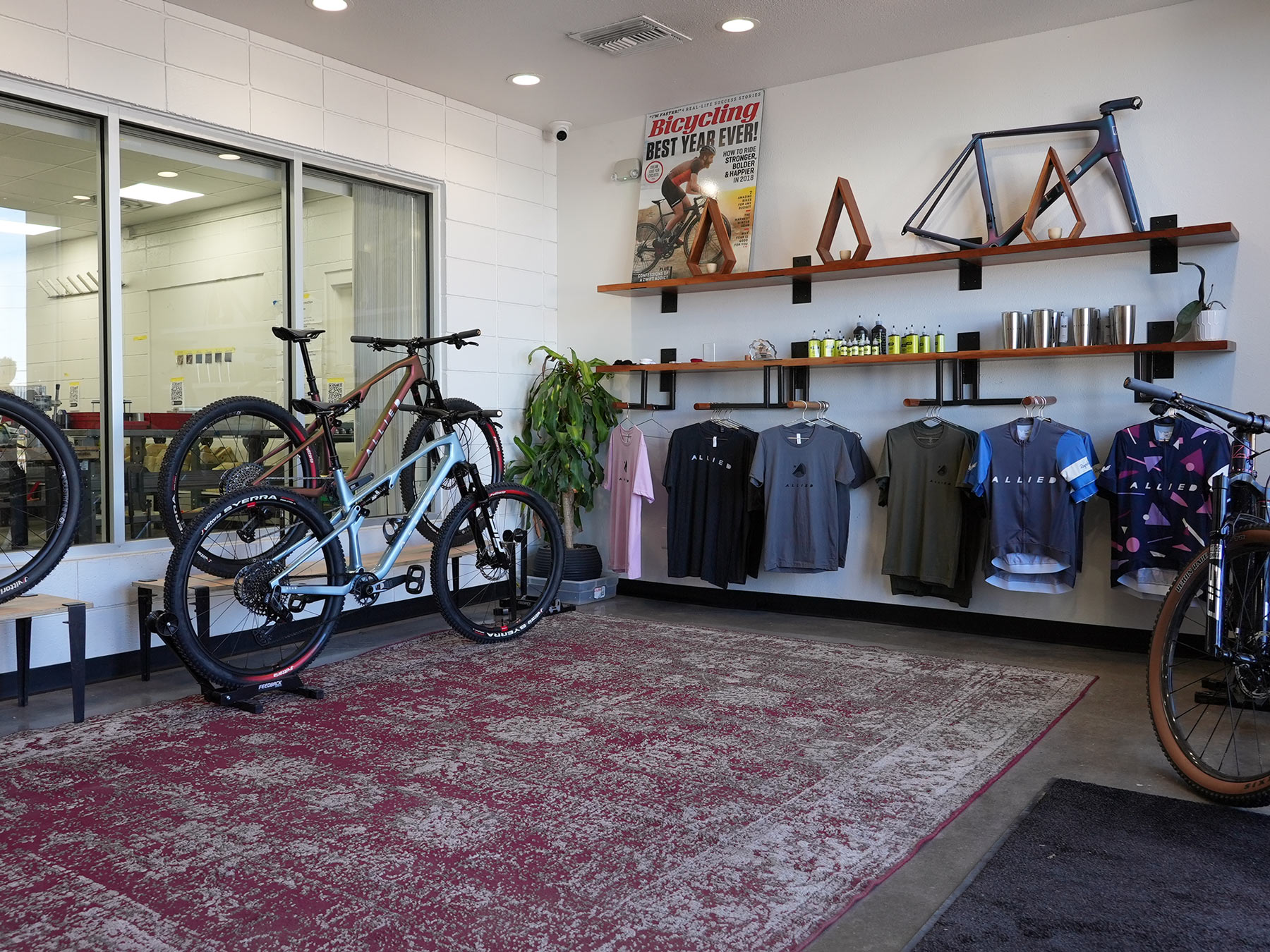
Enter the building and you’ll find their showroom, where you can see some of the bikes, check out merch, and pick up a demo bike. They keep a size run of each model available for test rides. Allied Cycle Works is also open for tours to anyone, just make a reservation in advance if you’d like to walk through this process in person.
Carbon Layup
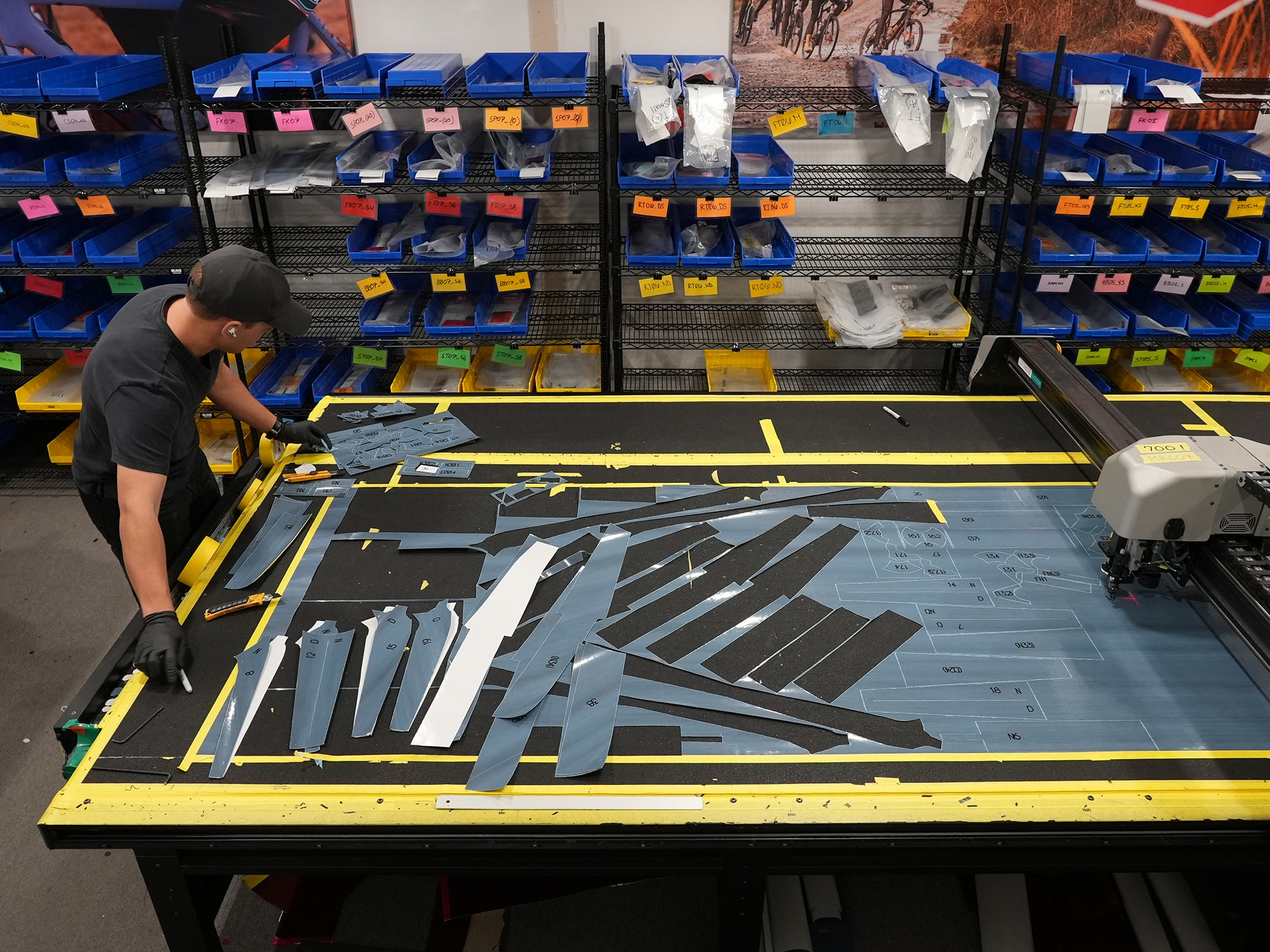
The first step in making the frames is cutting the carbon. They have an automated cutter that reads a computer program to minimize waste. Each frame section is cut in a group then bagged together and kitted in the trays and racks.
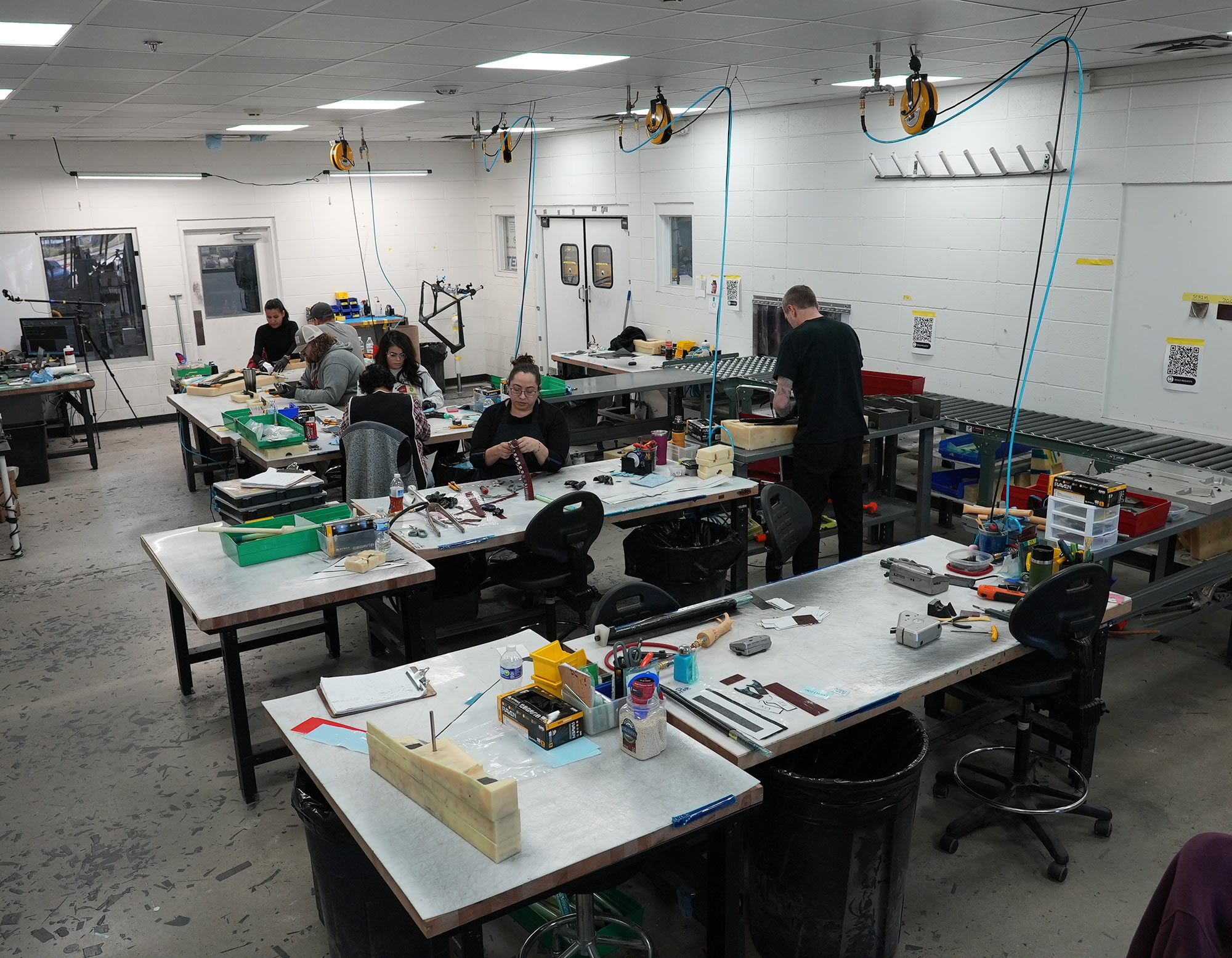
From there it goes into the layup room, where employees layup one tube or section at a time.
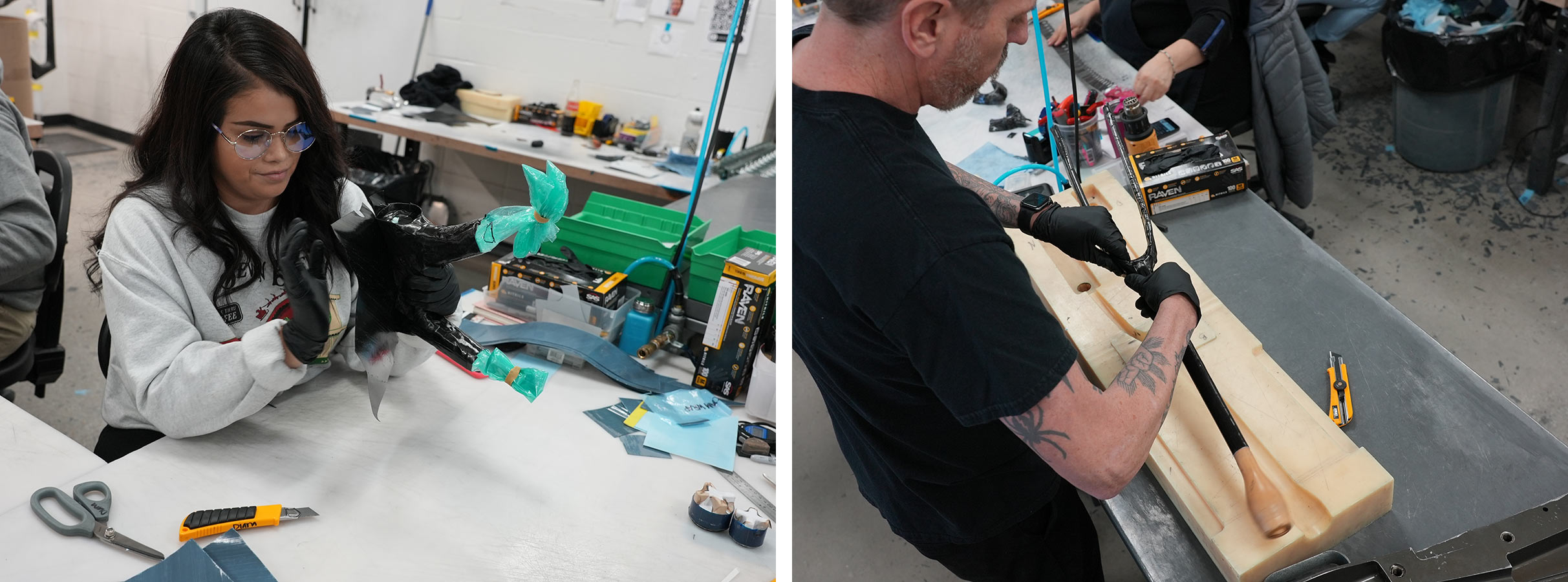
Each person is trained on one part of the bike for at least six weeks, becoming an expert at that part’s layup.
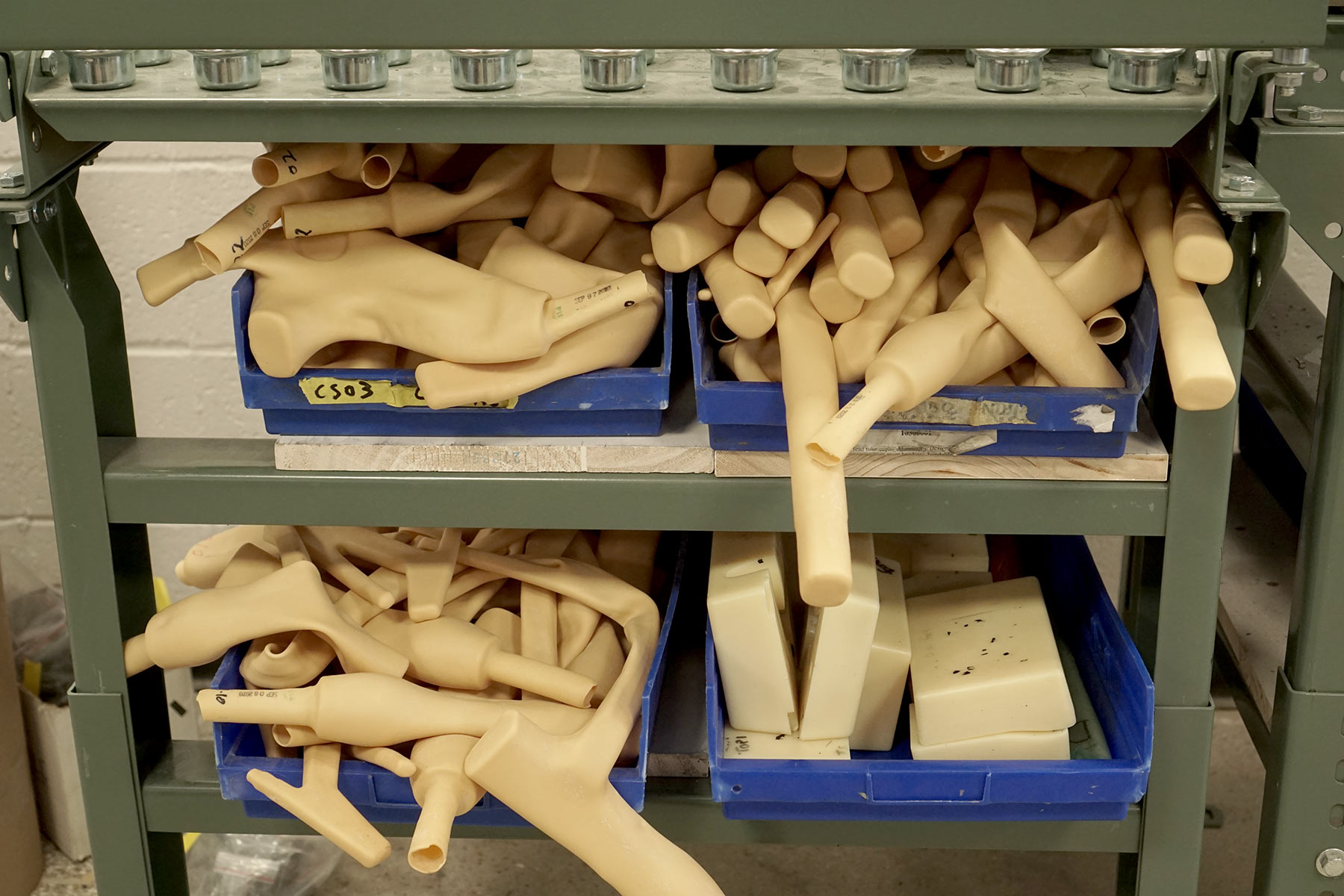
The carbon pieces are laid up over soft, reusable silicone mandrels.
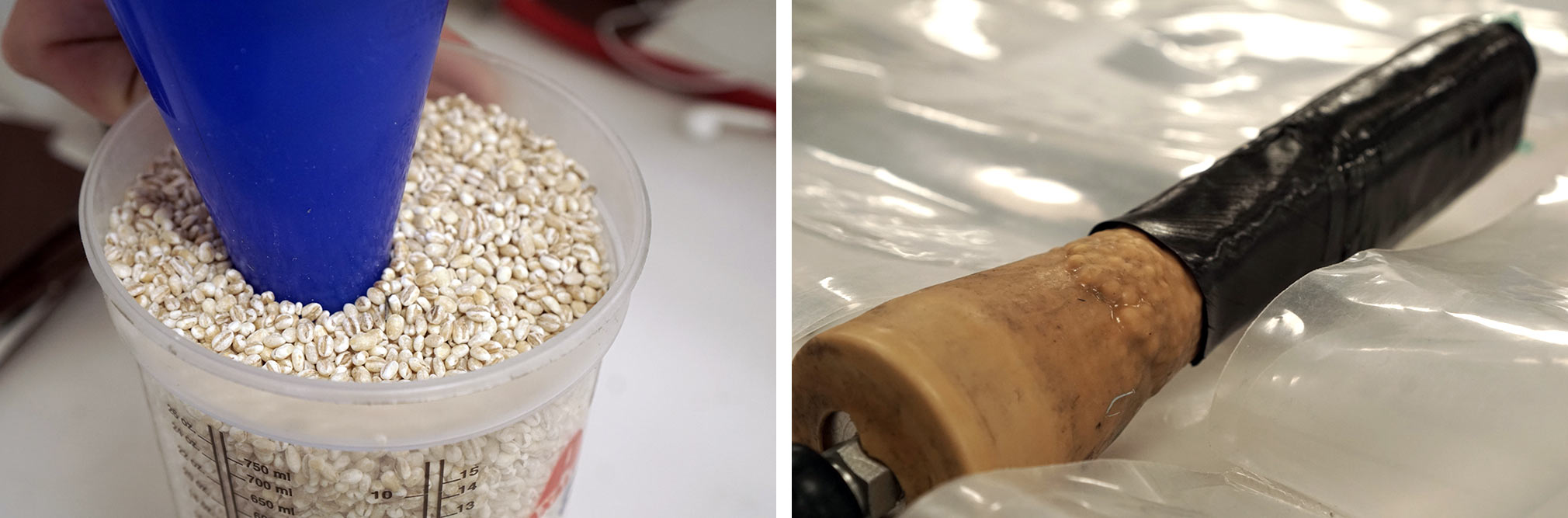
To make them firm enough to wrap carbon around, they fill them with grains. This gives them just enough shape for laying up the pre-preg carbon fiber, and once that’s done, the grains are dumped back out so that the molds can be pumped full of air once they go into the press.
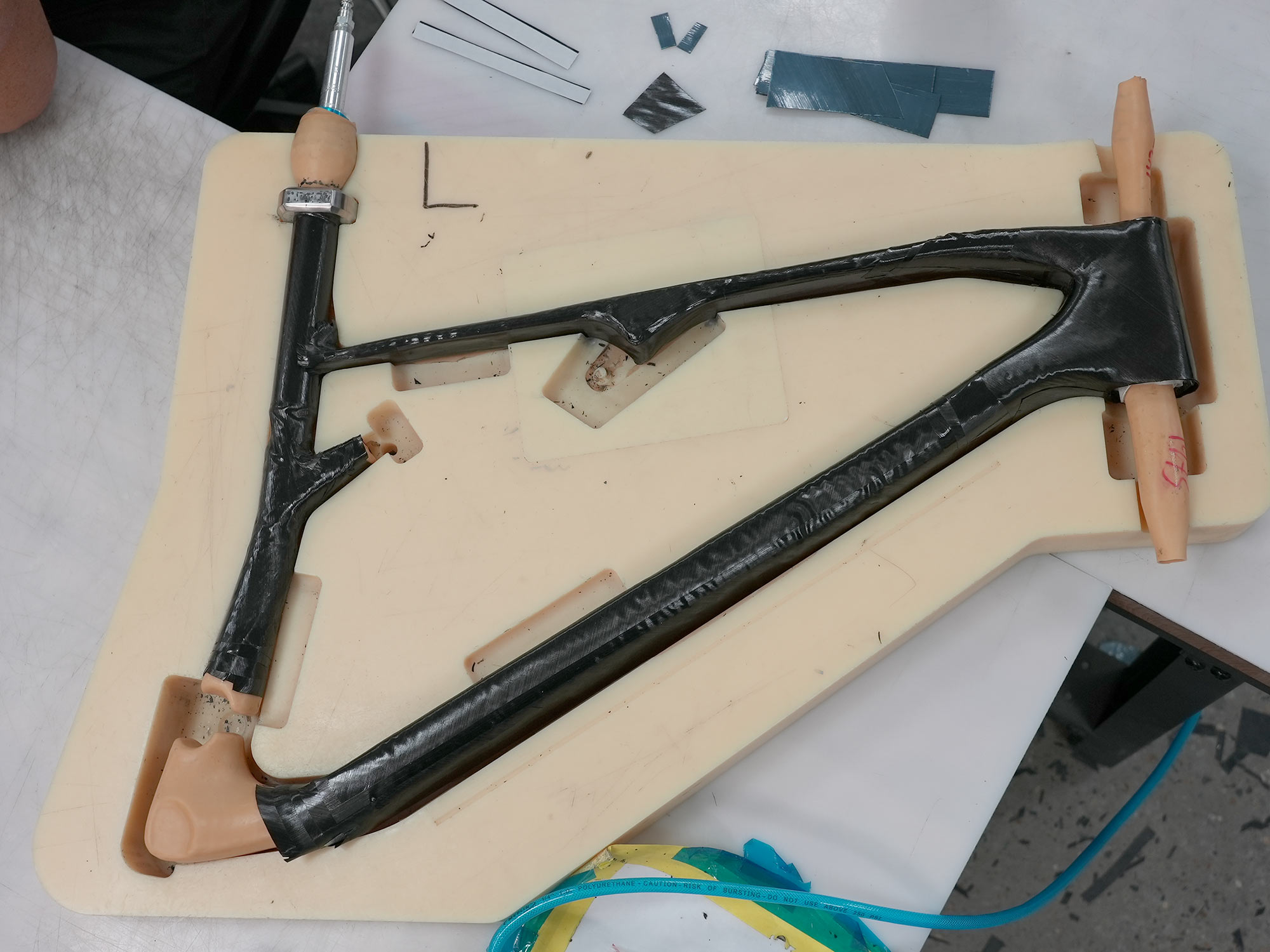
Each mandrel has a port where high-pressure air can go in, which will press the inner mold against a CNC machined aluminum outer mold.
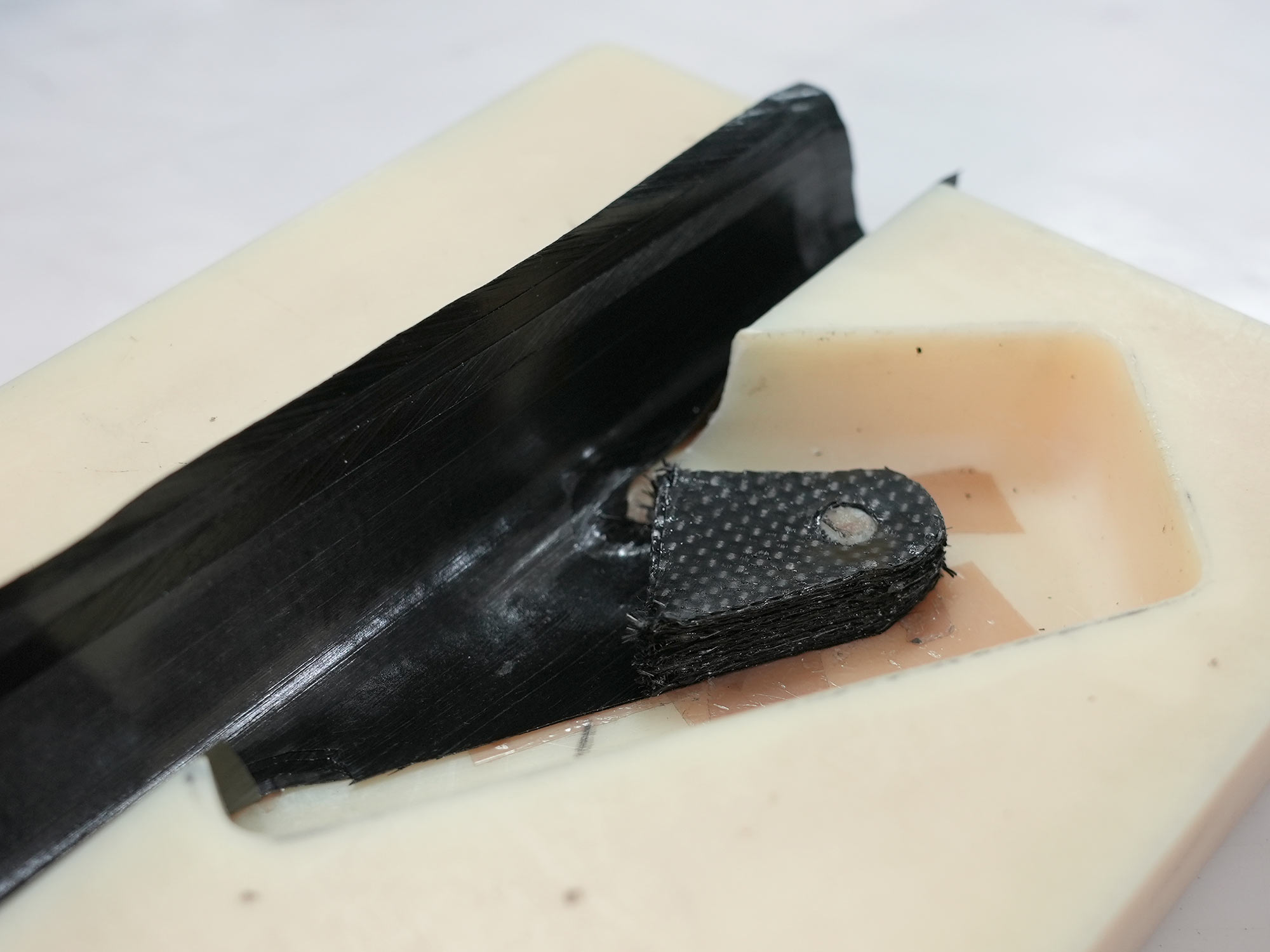
Some small parts and joints, like the BC40’s shock mount, are made by stacking layers of 3K woven carbon rather than the UD sheets used for most of the frame.
To the Presses
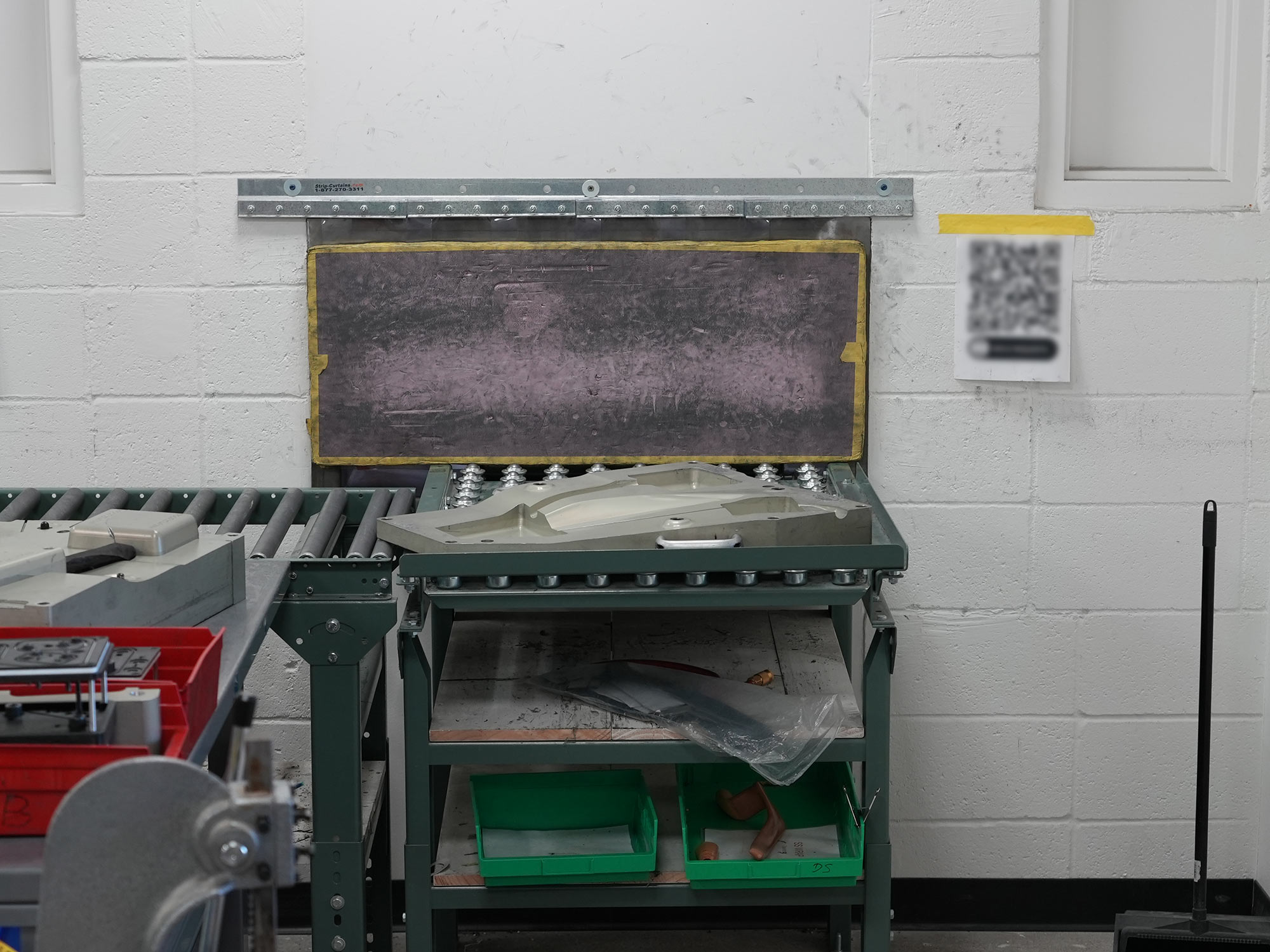
Once it’s all pieced together and in the mold, it passes through this door into…
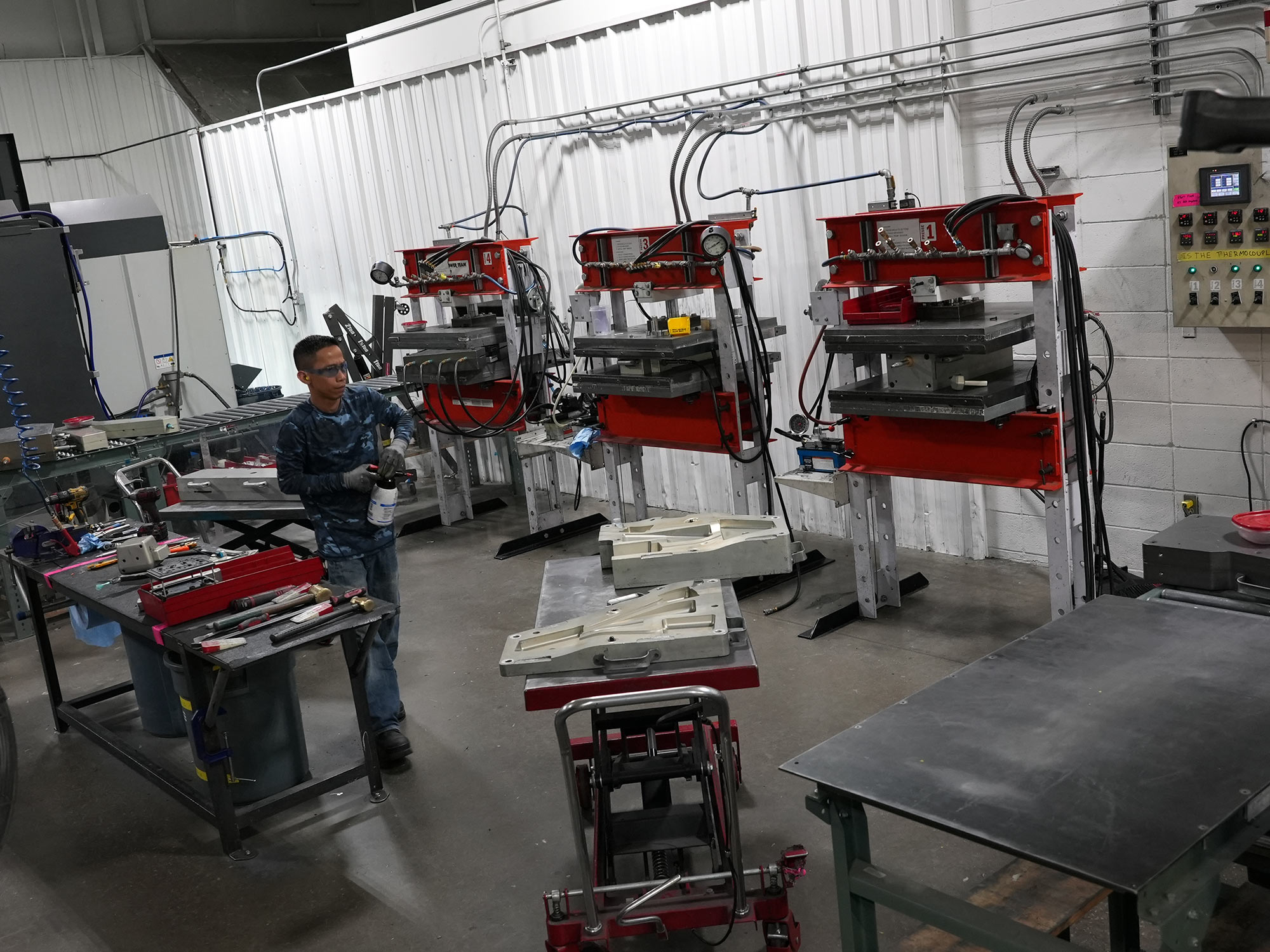
…the press room. Here, the molds are hooked up to the air lines and inserted into heat presses. These warm the insides to melt the resin while the air pressure squeezes the carbon layers against the metal mold. This pushes out any air and excess resin and essentially glues all of the layers together permanently.
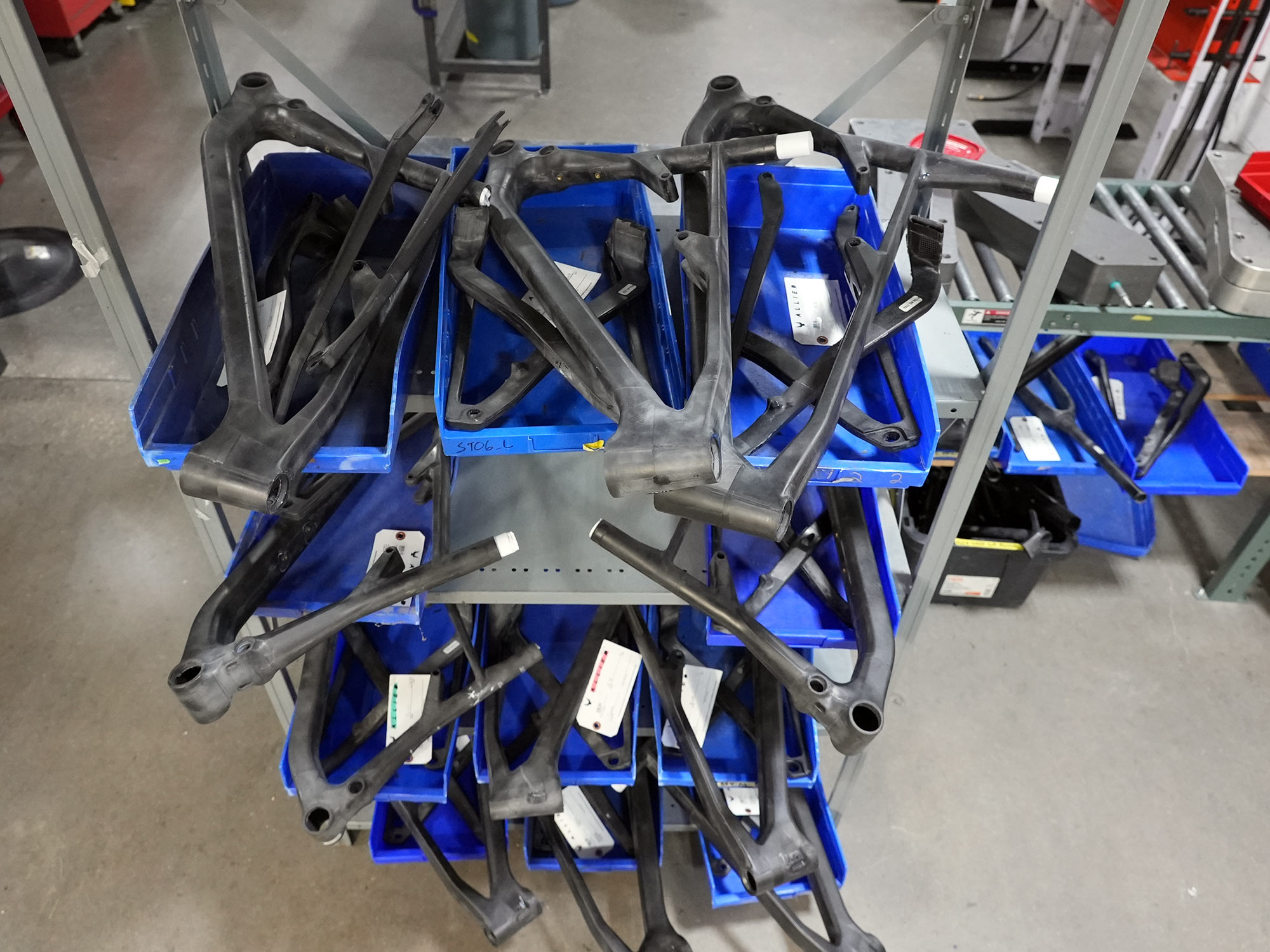
Once it cools, the molds are open, and out pops the frame part. In the case of the BC40, the entire front triangle is made as a single piece, and each side of the rear triangle is one piece.
Bonding
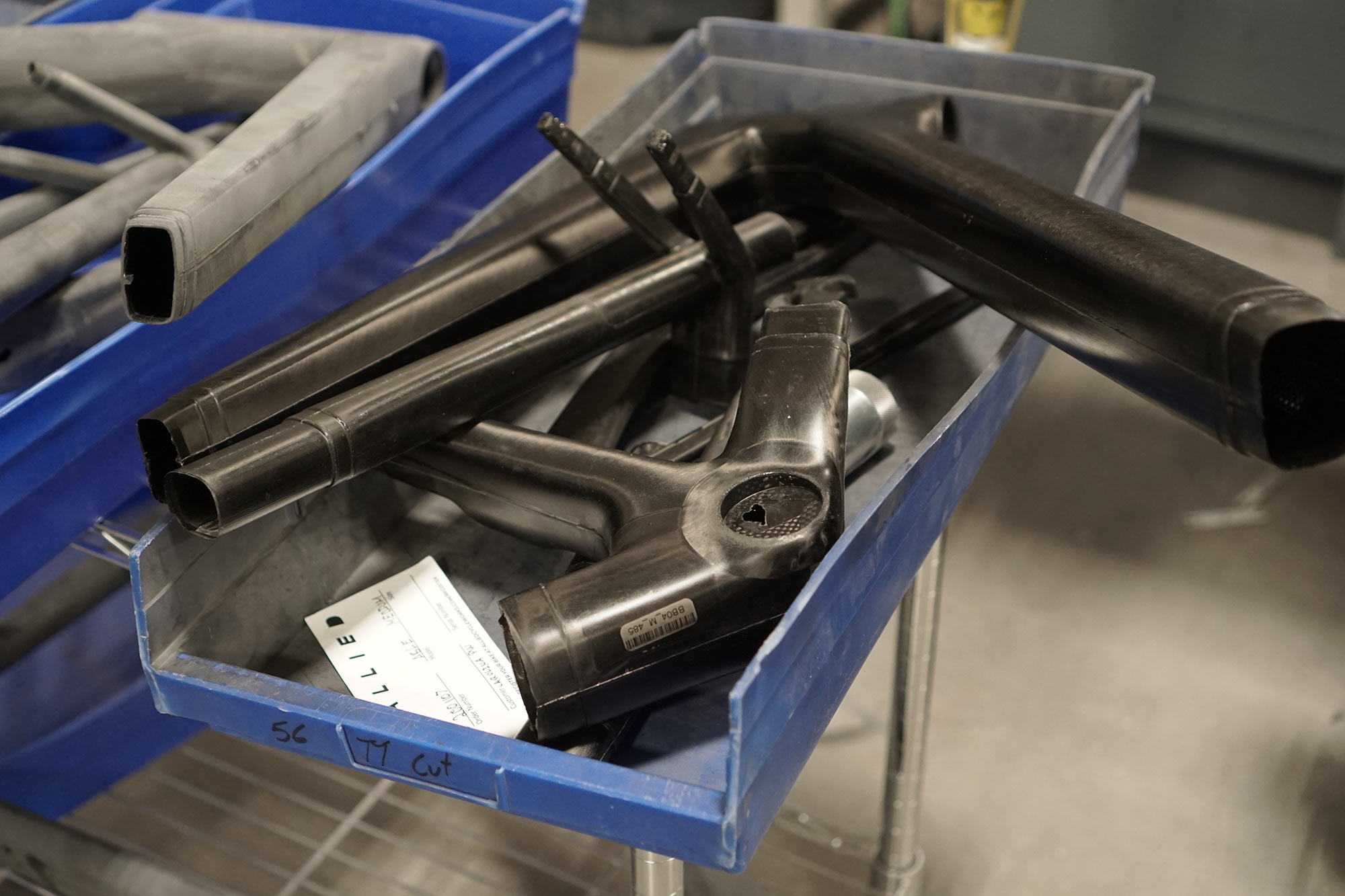
The road and gravel frames are made in sections, then bonded together. All of the parts are made in batches and kitted together, then they move over to the next area to be assembled and have any metal parts bonded into place.
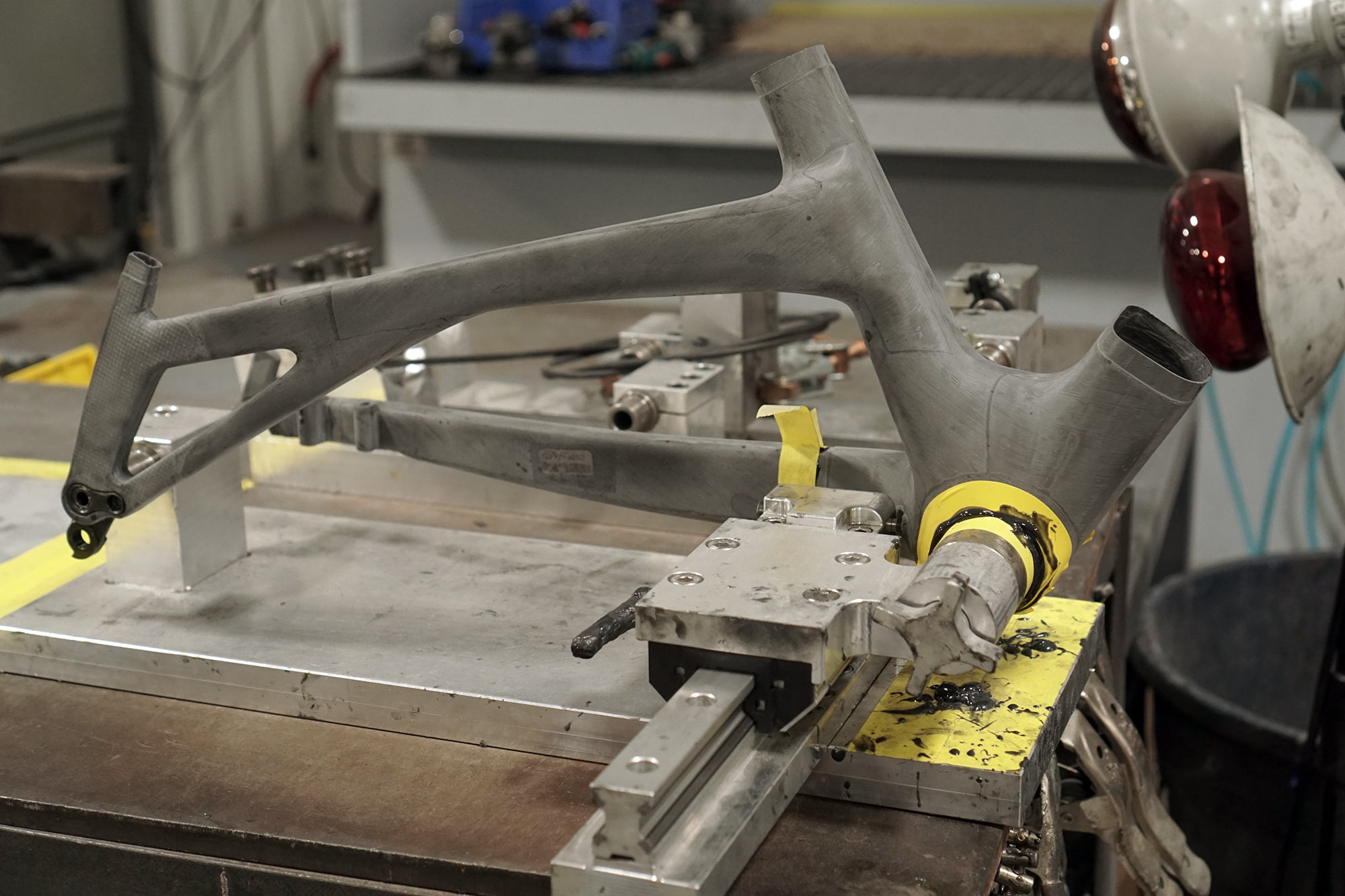
Allied uses metal threaded bottom brackets, and those are bonded into place to permanently attach inside the BB shell.
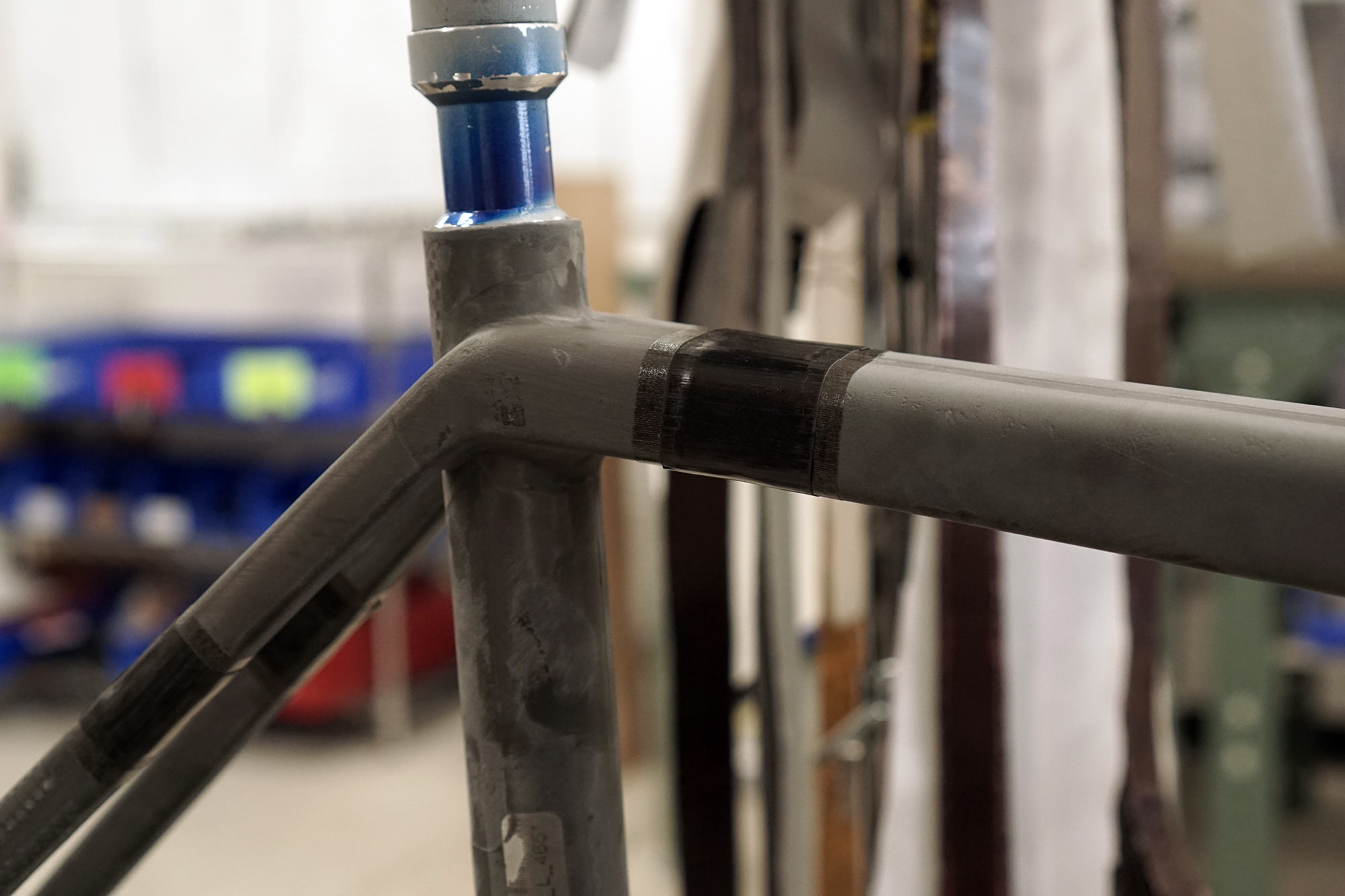
The tubes are sleeved to fit together. They use a bonding agent to glue them together, then overwrap each joint with a layer of carbon fiber. Then it’s back into an oven to cure the bonding glue and overwrap, essentially creating one single unit.
Quality Control

Once the frame looks like a frame, it goes through a series of checks for alignment and cable pass-through. Now is the time to fix any little issues. They want to make sure all of the hoses, wires, and cables will slide all the way through any internal routing ports before the frame gets sanded and painted!
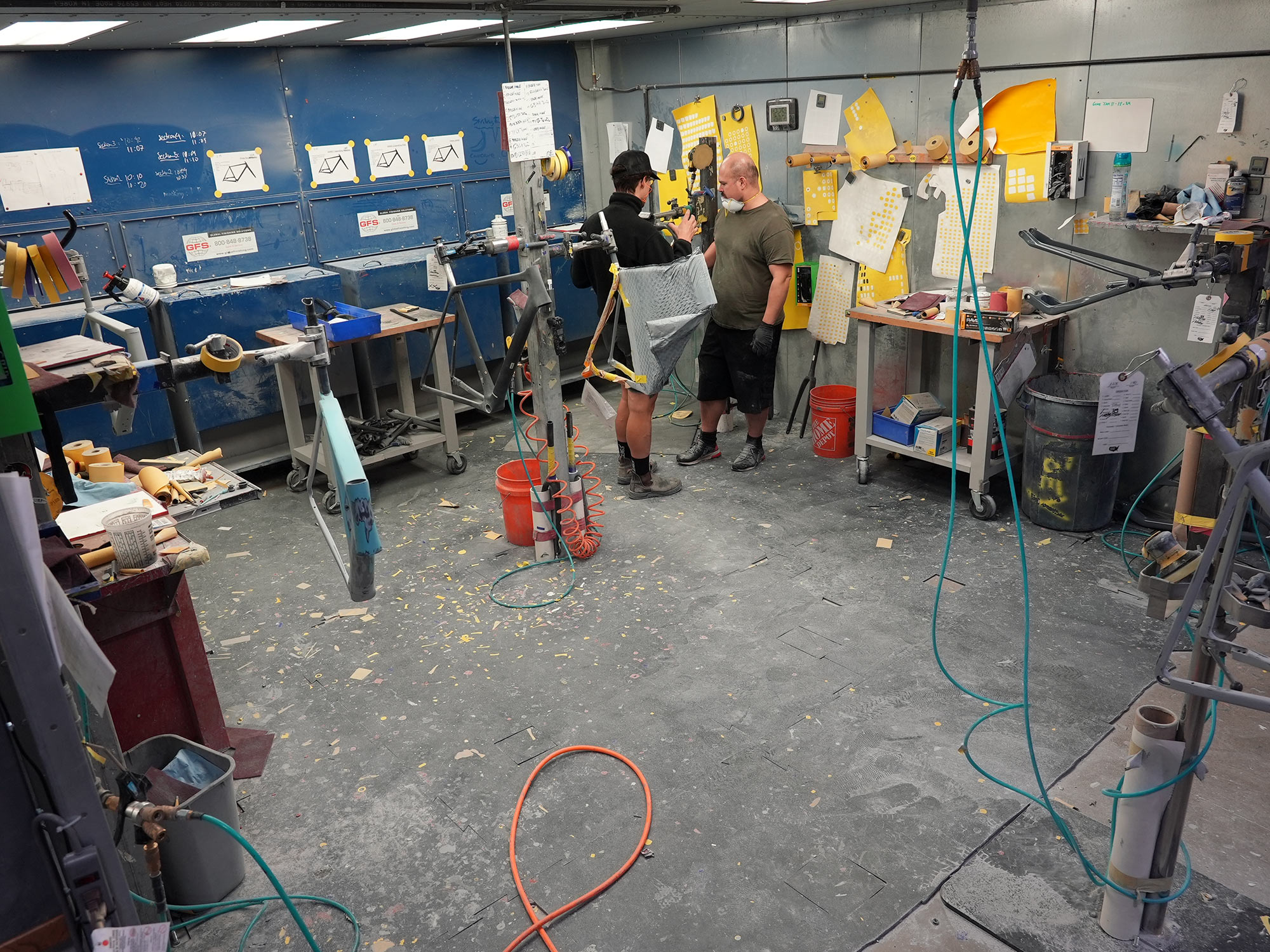
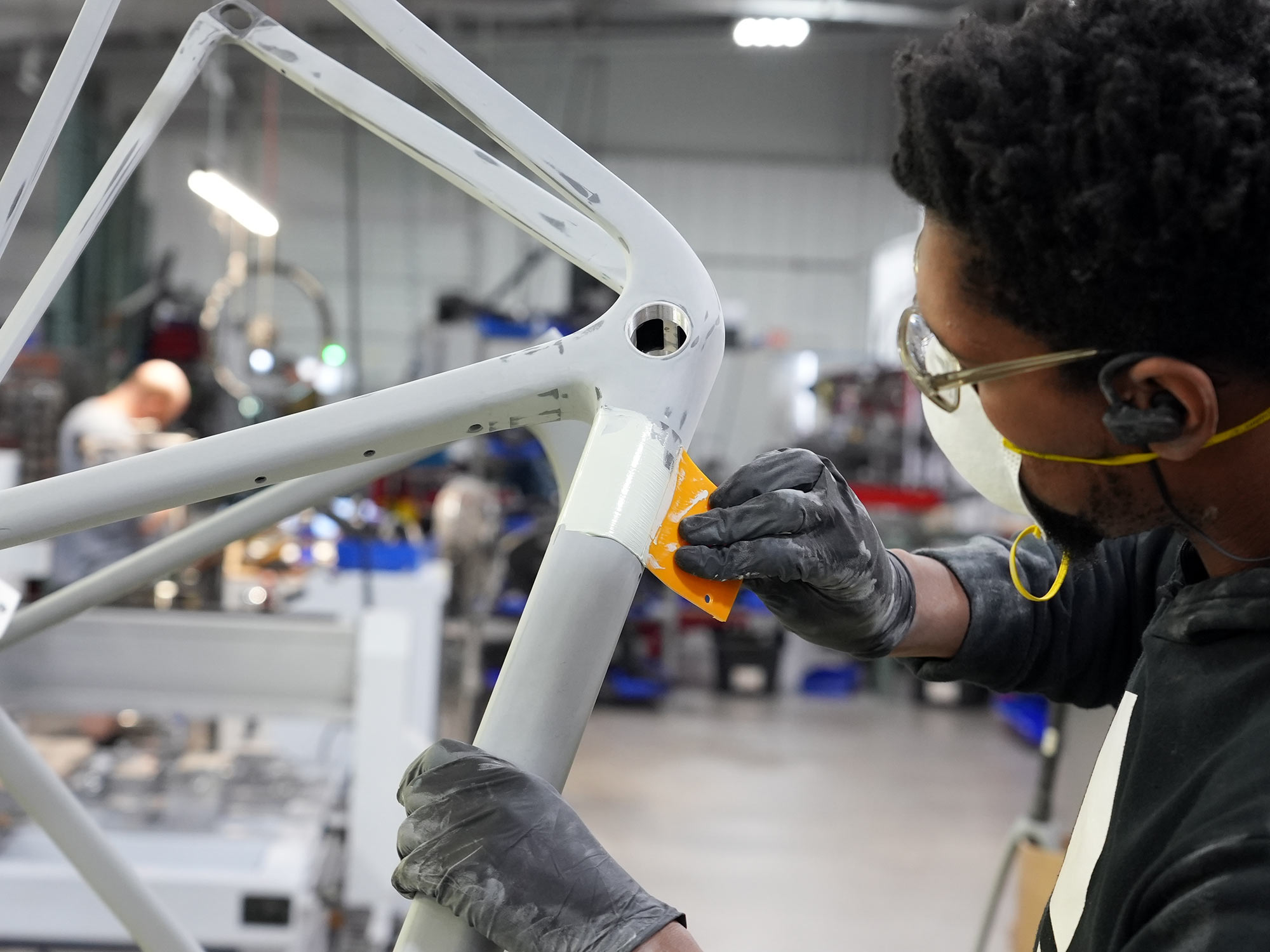
Once it passes that QC check, it moves on to sanding and finishing. All flashing is removed, and the frames are coated in a lightweight filler to smooth any small imperfections from the molding process. This is done so that they have a layer to sand smooth before paint without having to sand the carbon. That’s important because Allied doesn’t add a cosmetic outer layer of carbon fiber, and they can’t sand the carbon itself. So this filler is applied all over the frame, and then mostly sanded off.
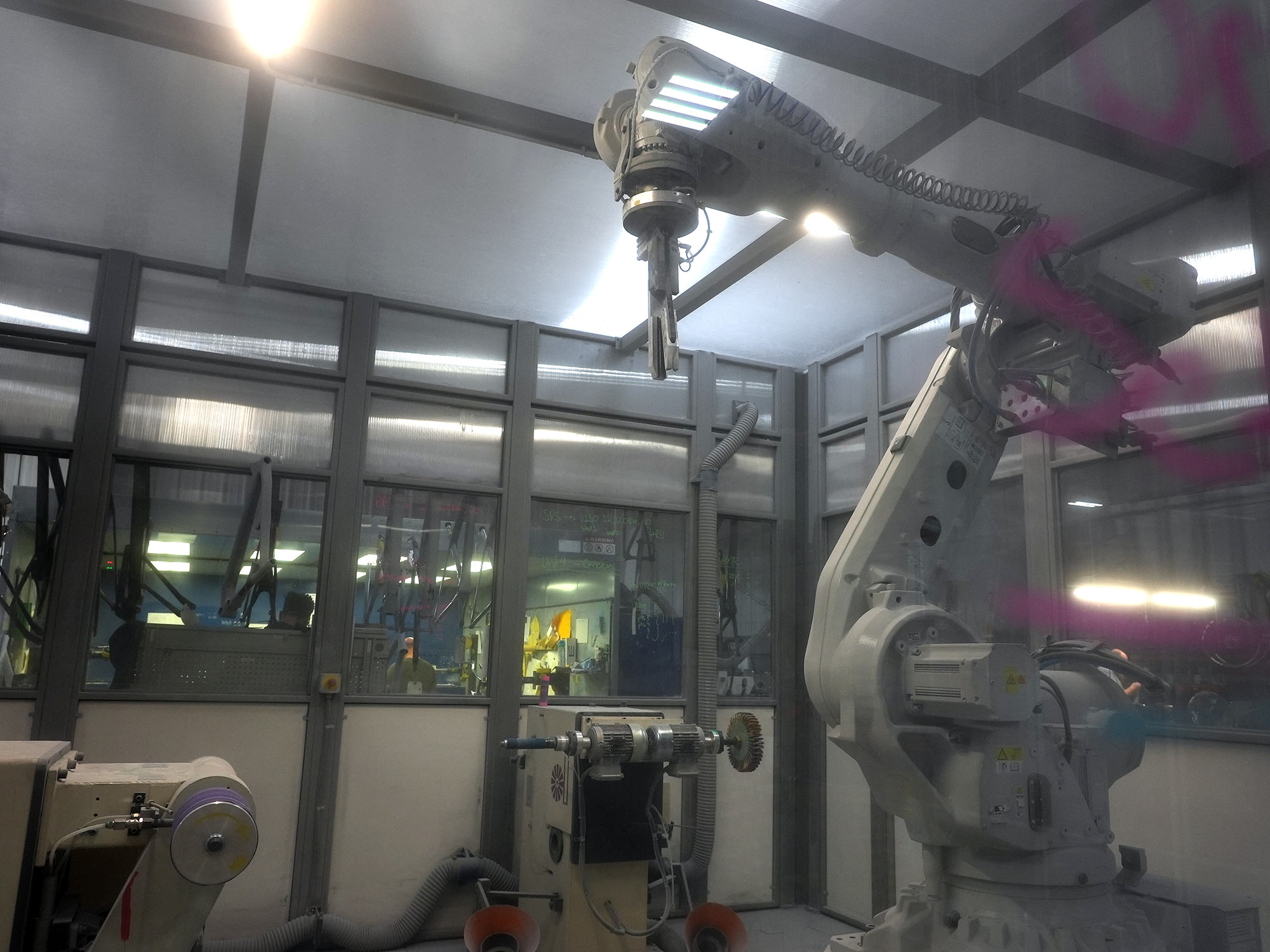
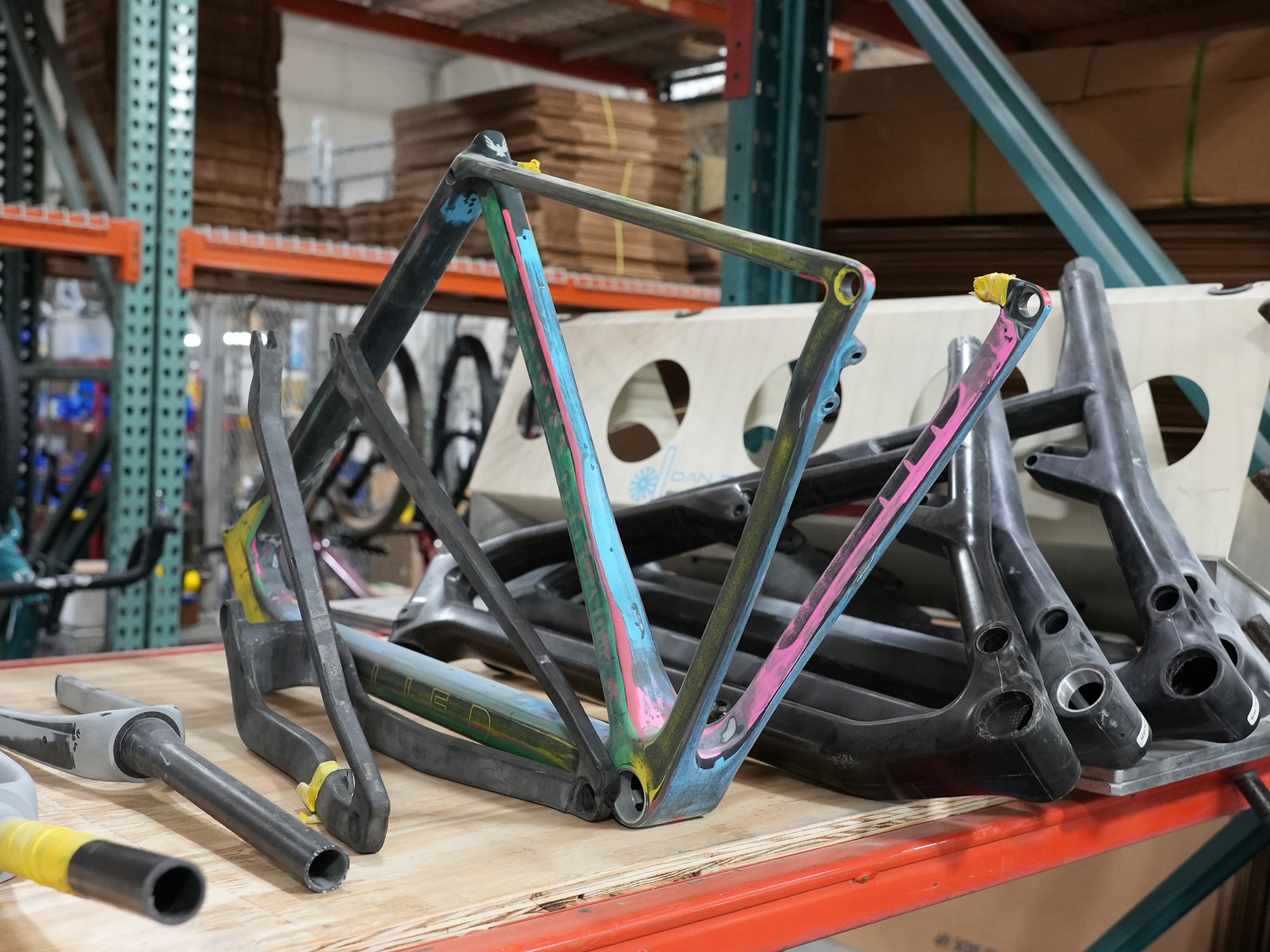
Finishing
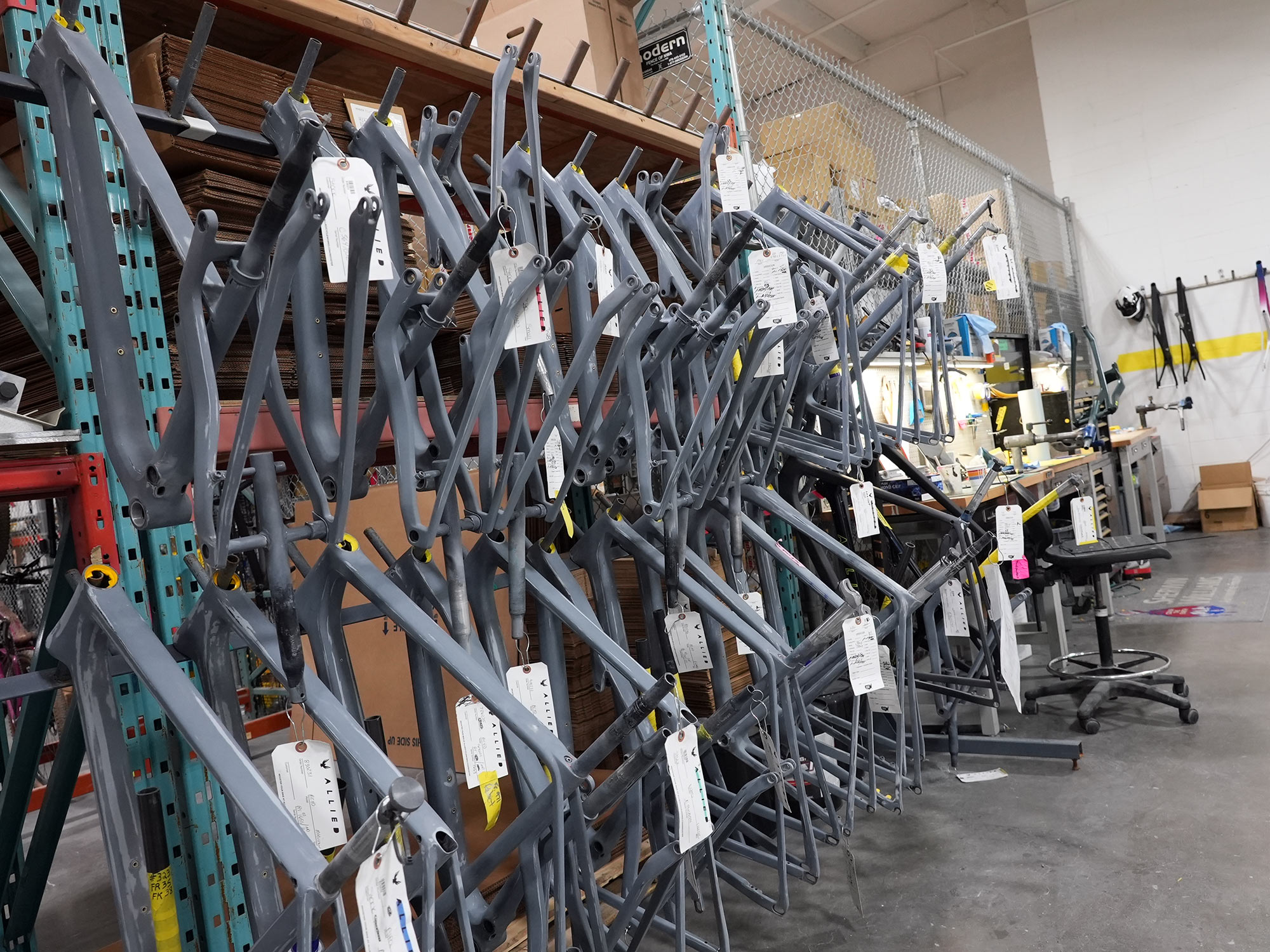
Once that’s done, the frames are ready for painting. Shown above are bikes ready for their first layer of paint, which will become the color of any logos or graphics.
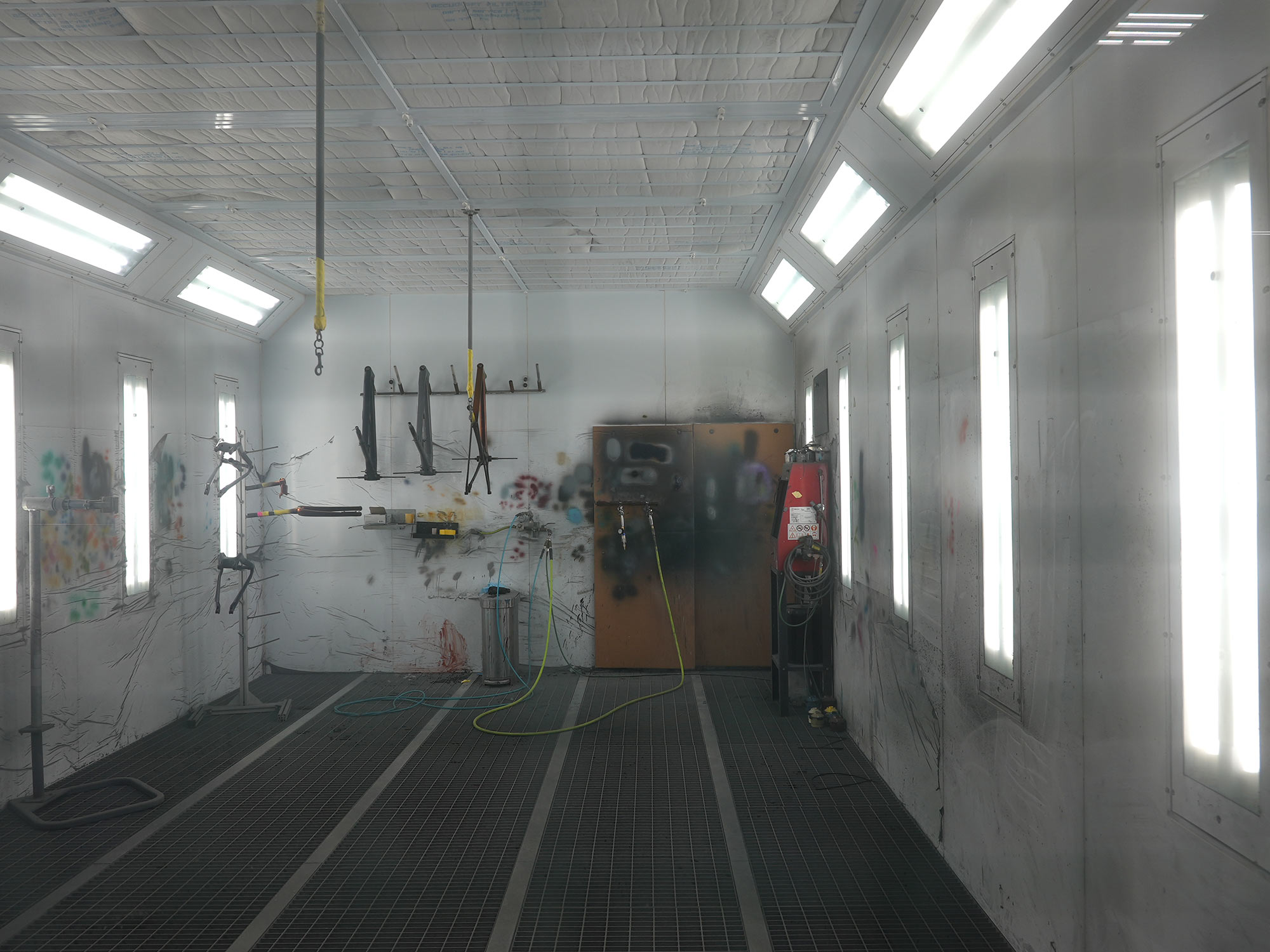
Allied paints all of their logos using a two-step process. First, they paint a base coat color that will show up as the logos. After that’s dry, vinyl graphics are applied to mask off the logos, then it goes back in the paint booth for the final (outer) paint color.
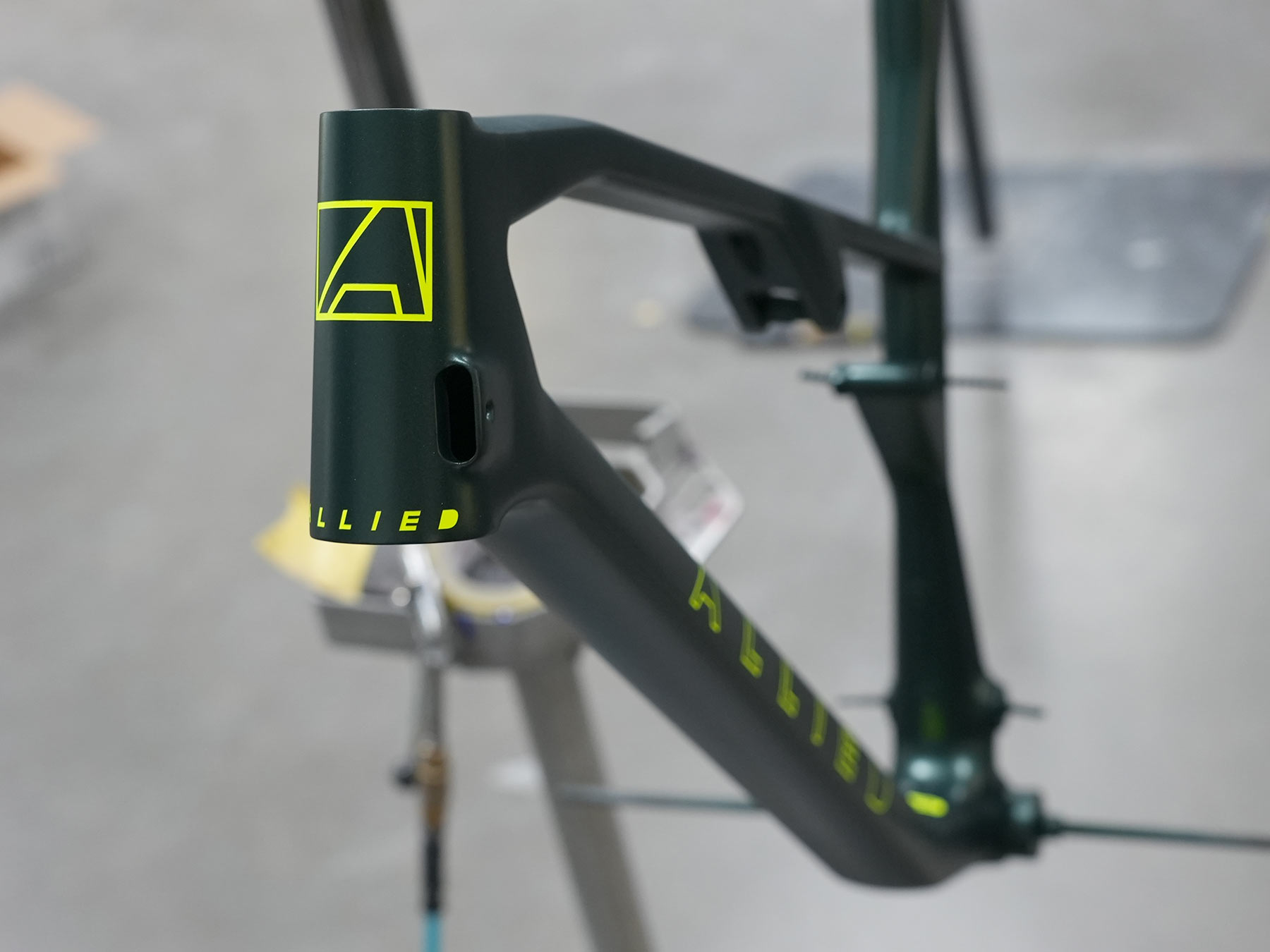
Once that coat is dry, the masking stickers are pulled off, revealing the logos. So, for this bike above, it was painted neon yellow first, then masked, then painted in racing green. Removing the masking revealed the bright yellow logos. There are no decals on the finished product, it’s all paint. (Side note: The use of filler for sanding and smoothing is why Allied doesn’t offer frames unpainted or showing the raw carbon)
Assembly & Shipping
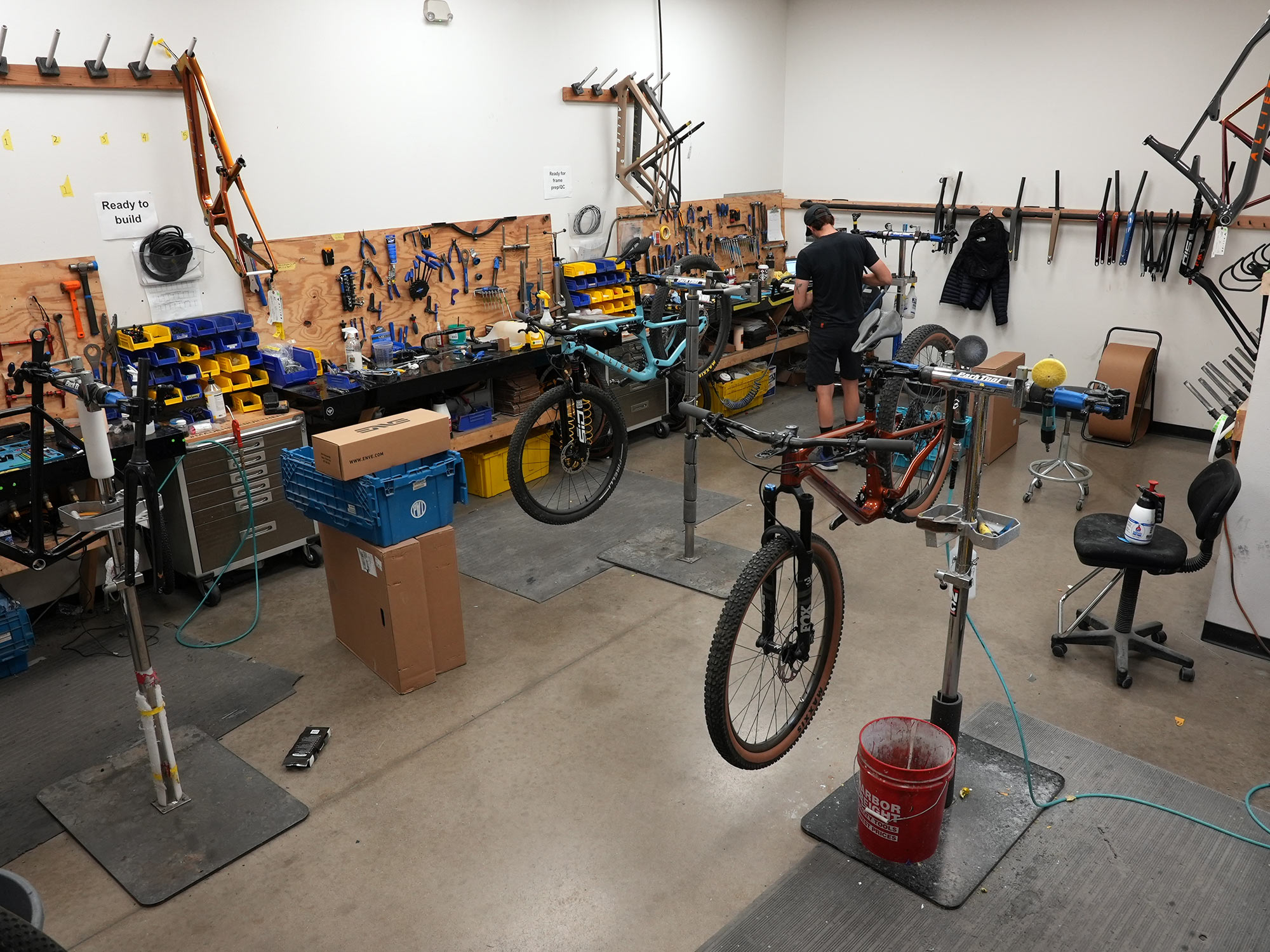
Once they’re painted and check, they move into the assembly room. Allied sells to shops and sells direct, but they’re all assembled in this room.
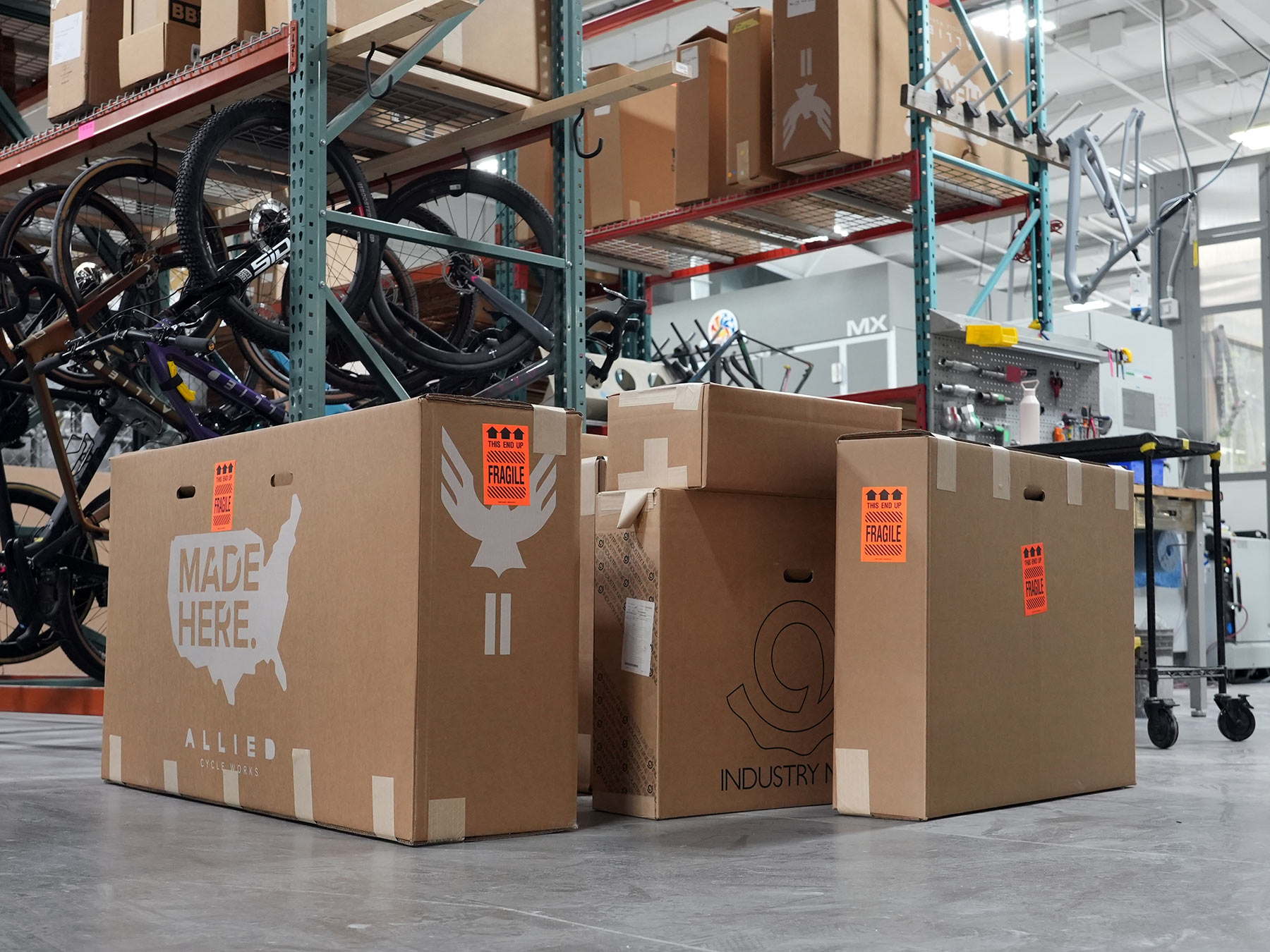
Then they’re boxed and ready for pickup, heading to a happy rider somewhere!
Huge thanks to Will, Drew, Cole, and the rest of the crew for showing us around and taking us for a ride!